Dokumenterede resultater og effekter
Dyk ned i detaljerede analyser af, hvordan vores CNC-bearbejdningstjenester har haft en positiv indvirkning på vores kunders drift. Disse casestudier viser håndgribelige fordele som omkostningsreduktion, forbedret ydeevne og hurtigere produktionstider.
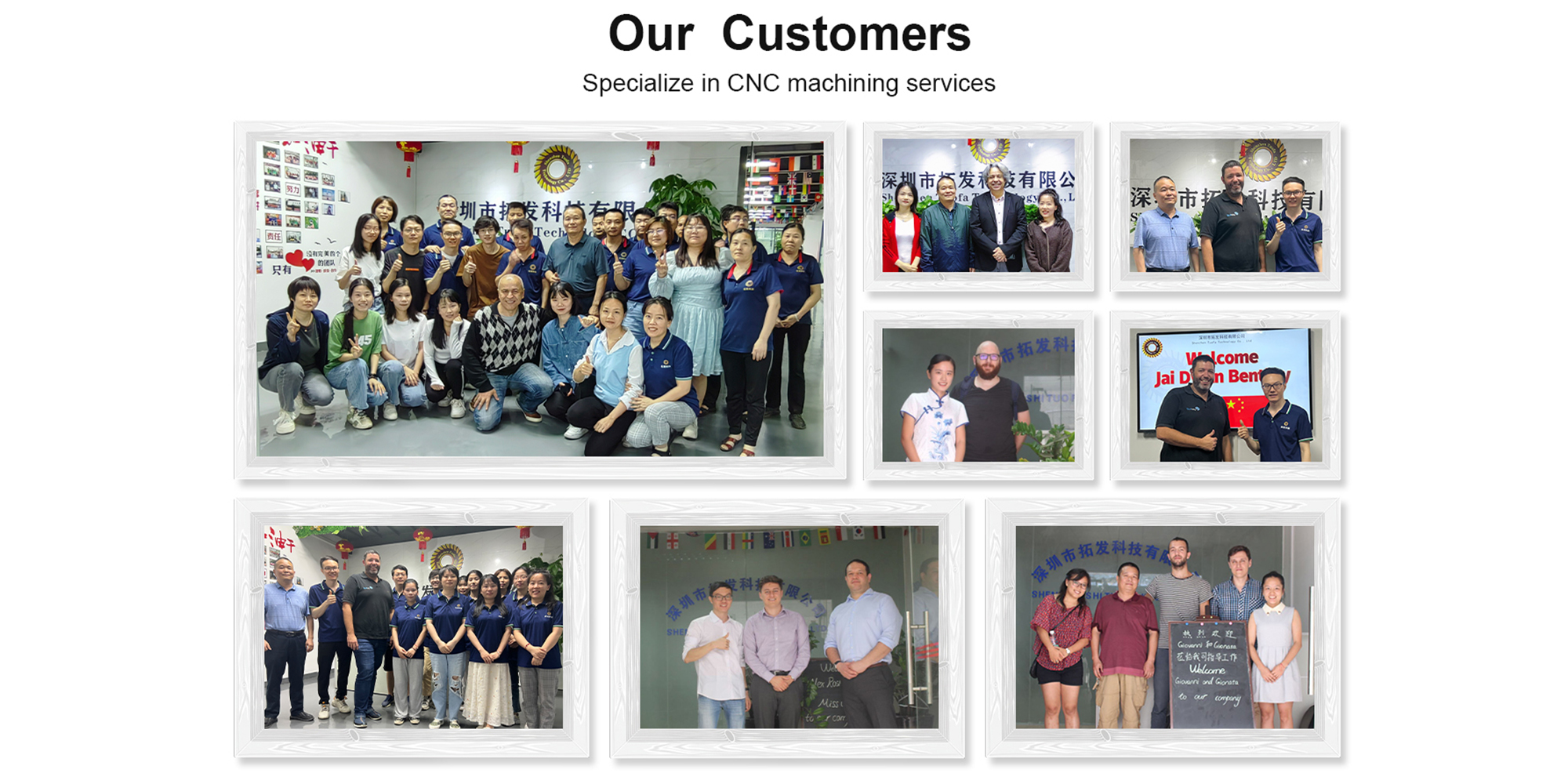
Casestudie 1: Designoptimering og omkostningsreduktion
Udfordring: En kunde inden for rumfart havde brug for en kompleks komponent, men det oprindelige design var uoverkommeligt dyrt at producere.
Løsning: Ved at implementere DFM-principper (Design for Manufacturing) redesignede vores ingeniørteam komponenten for at forenkle fremstillingsprocessen. Denne tilgang minimerede materialeforbruget og strømlinede produktionstrinnene uden at gå på kompromis med ydeevnen.
Resultat:
Økonomisk indvirkning: Kunden var i stand til at markedsføre sit produkt til en konkurrencedygtig pris og øgede sin markedsandel med 10% på grund af omkostningseffektiviteten og den hurtige tilgængelighed af komponenterne.
Casestudie 2: Hurtig etablering af produktionslinje
Udfordring: En leverandør af bildele havde brug for hurtigt at masseproducere en kritisk komponent på grund af en afbrydelse i forsyningskæden.
Løsning: Vi mobiliserede vores ressourcer til at køre vores CNC-maskiner 24/7 og prioriterede dette projekt frem for andre for at imødekomme kundens presserende behov.
Resultat:
Økonomisk indvirkning: Kunden undgik et anslået salgstab på $2 millioner ved at opretholde driften af produktionslinjen uden afbrydelser.
Casestudie 3: Innovativ materialeanvendelse
Udfordring: En producent af medicinsk udstyr havde brug for et korrosionsbestandigt og biokompatibelt materiale til kirurgiske værktøjer.
Løsning: Vi anbefalede en legering af rustfrit stål af høj kvalitet, der er kendt for sin holdbarhed og kompatibilitet i medicinske anvendelser. Der blev brugt præcisions-CNC-bearbejdning for at opfylde de strenge medicinske standarder.
Resultat:
Økonomisk indvirkning: Reducerede omkostninger til udskiftning af værktøj og øget salg på grund af produktets overlegne ydeevne og pålidelighed.
Casestudie 4: Hurtig prototyping af komplekse komponenter
Udfordring: En teknologivirksomhed havde brug for hurtig prototyping til at teste nye højtydende komponenter til sportsudstyr.
Løsning: Vi brugte vores avancerede CNC-maskiner til hurtigt at producere nøjagtige og komplekse prototyper til designvalidering.
Resultat:
Økonomisk indvirkning: Kunden reducerede de samlede F&U-omkostninger med 15% og øgede konkurrenceevnen på markedet ved at lancere produktet før konkurrenterne.
Casestudie 5: Anvendelse af marine komponenter og miljøtilpasning
Udfordring: En kunde med speciale i marineudstyr havde brug for en holdbar komponent, der kunne modstå barske havmiljøer, til deres udstyr til dybhavsudforskning. Komponenten skulle kunne modstå korrosion i saltvand, trykvariationer og ekstreme temperaturer, hvilket var afgørende for sikkerheden og effektiviteten i driften.
Løsning: Vi valgte en titaniumlegering af høj kvalitet, som giver overlegen styrke, korrosionsbestandighed og letvægtsegenskaber, der er ideelle til marineanvendelser. Vores team brugte avancerede CNC-bearbejdningsteknikker for at opnå præcision i fremstillingsprocessen. Vi brugte også et dobbeltbelægningssystem: et basislag af epoxy af marinekvalitet efterfulgt af et toplag af fugthærdet urethan, der forbedrer komponentens modstandsdygtighed over for saltvand og ultraviolet lys.
Resultat:
Økonomisk indvirkning: Kunden rapporterede en reduktion af vedligeholdelsesomkostningerne på 20% på grund af komponentens forbedrede holdbarhed og længere levetid. Derudover muliggjorde udstyrets forbedrede effektivitet og pålidelighed en stigning i driftstiden på 15%, hvilket øgede kundens produktivitet og rentabilitet betydeligt.