Custom Polypropylene(PP) Machining for Complex Designs
Utilize our custom polypropylene machining services to meet your unique design needs. Polypropylene is renowned for its toughness, chemical resistance, and low moisture absorption, making it ideal for durable and lightweight parts.
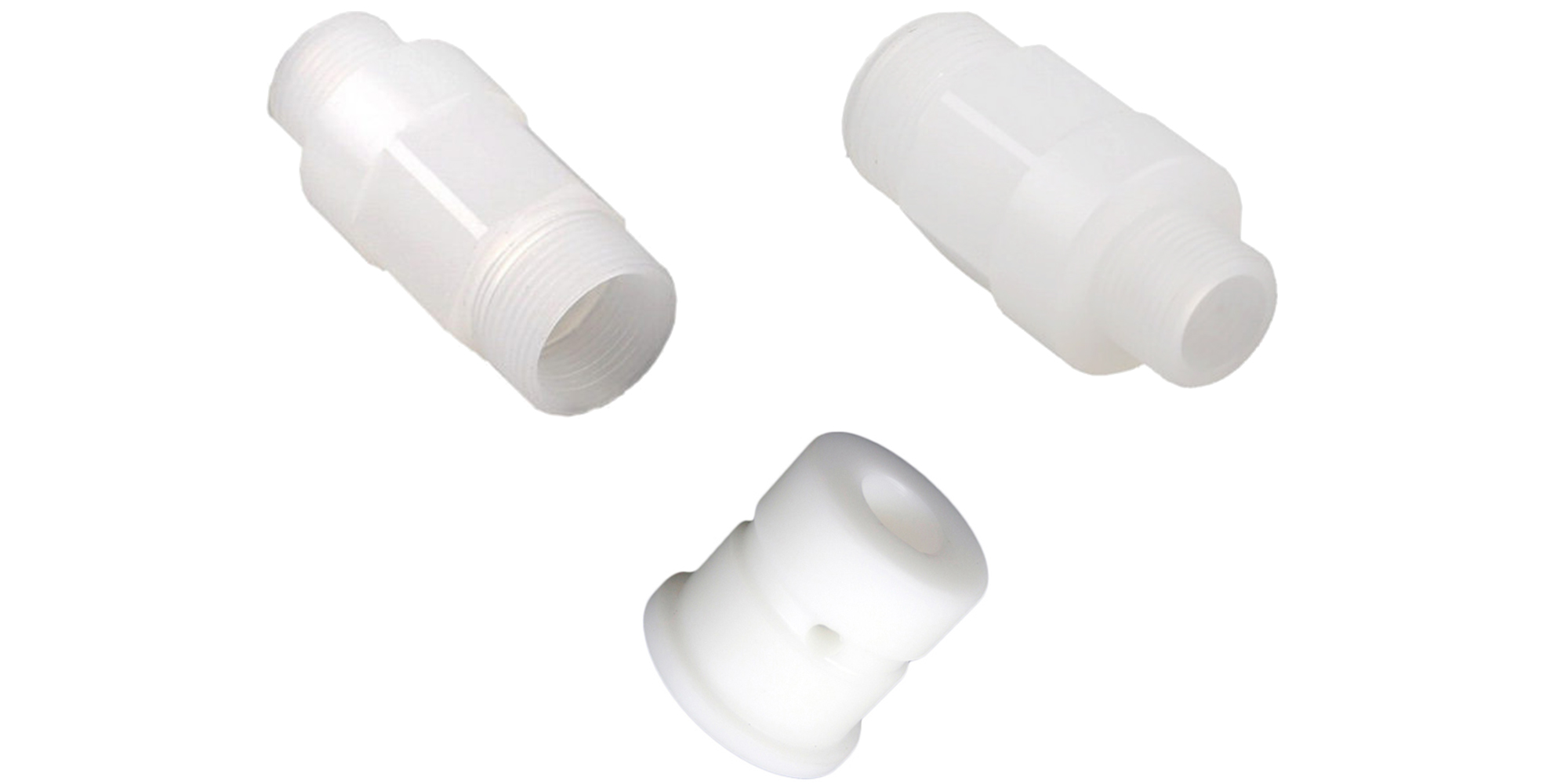
Advantages and Disadvantages of Polypropylene Machining Parts
Advantages | Disadvantages |
---|---|
Chemical Resistance | Low Softening Point |
Highly resistant to chemicals, suitable for chemical processing and lab containers. | Has a low softening point (around 150°C), limiting its use in high-temperature applications. |
Low Density | Poor UV Resistance |
Lighter than many plastics, beneficial for reducing weight in applications like automotive and medical devices. | Prone to degradation when exposed to UV light unless treated with stabilizers. |
Low Moisture Absorption | Difficulty in Painting and Bonding |
Absorbs very little water, ensuring performance stability in wet environments. | Non-polar and non-reactive surface makes it difficult to paint or bond without special treatments. |
Excellent Fatigue Resistance | Wear Resistance |
Good for repeated bending applications such as hinges and snap-fit parts. | Not as wear-resistant as some other plastics, limiting its use in high-abrasion environments. |
Cost-Effectiveness | Dimensional Stability |
Generally less expensive than many engineering plastics, ideal for bulk production. | Can deform under mechanical stress or thermal cycling, affecting precision applications. |
Polypropylene CNC Machining Parts and Applications
Polypropylene is a versatile thermoplastic widely used in CNC machining to produce various parts due to its favorable properties.
PP Copolymer vs Homopolymer: What’s the Difference?
Polypropylene (PP) is available in several forms, the two most common being homopolymer and copolymer. Understanding the differences between these types can help in selecting the right material for specific applications. Here’s a breakdown of the main differences between PP homopolymer and copolymer:
Property/Aspect | PP Homopolymer | PP Copolymer |
---|---|---|
Composition | Polymerized from a single monomer, propylene. | Polymerized from propylene with ethylene or butene. |
Stiffness | Higher stiffness, suitable for rigid applications. | Lower stiffness, beneficial for flexible applications. |
Tensile Strength | Higher tensile strength, handles more elongation load. | Lower tensile strength than homopolymers. |
Impact Resistance | Lower impact resistance, especially at low temperatures. | Improved impact resistance, even at low temperatures. |
Temperature Resistance | Higher, suitable for high-temperature applications. | Slightly lower, not optimal for very high temperatures. |
Chemical Resistance | Excellent, similar to copolymers. | Excellent, suitable for various chemical environments. |
Stress Crack Resistance | Lower resistance to stress cracking. | Better resistance to stress cracking. |
Typical Applications | Food packaging, automotive parts, reusable containers. | Living hinges, automotive bumpers, medical components. |
Physical Properties of PP Plastic
These physical properties indicate that PP Homopolymer is better suited for applications that require higher temperature resistance and stiffness, while PP Copolymer is more appropriate for applications where lower temperatures and higher impact resistance are critical.
Physical Property | PP Homopolymer | PP Copolymer |
---|---|---|
Density (g/cm³) | Approximately 0.905 | Approximately 0.900 |
Melting Point (°C) | 160-165 | 135-159 |
Tensile Strength (MPa) | 30-35 | 25-30 |
Modulus of Elasticity (MPa) | 1500-1600 | 1200-1300 |
Impact Strength | Lower, particularly at low temperatures | Higher, good toughness at low temperatures |
Thermal Expansion (x 10^-6/°C) | 100-150 | 100-150 |
Key Considerations for CNC Machining Polypropylene
When CNC turning or CNC milling polypropylene, there are several critical considerations to ensure optimal outcomes:
Post-processing for Polypropylene CNC Parts
Polypropylene is easy to machine due to its softness. But you must watch the temperature to avoid melting it. Additionally, polypropylene can produce long, stringy chips that may need frequent clearing to avoid interference with ongoing machining operations.