Achieve Optical Clarity with Polycarbonate CNC Machining
Enhance the visual appeal and functionality of your products with our polycarbonate(PC) machining that maintains the material’s inherent optical clarity.
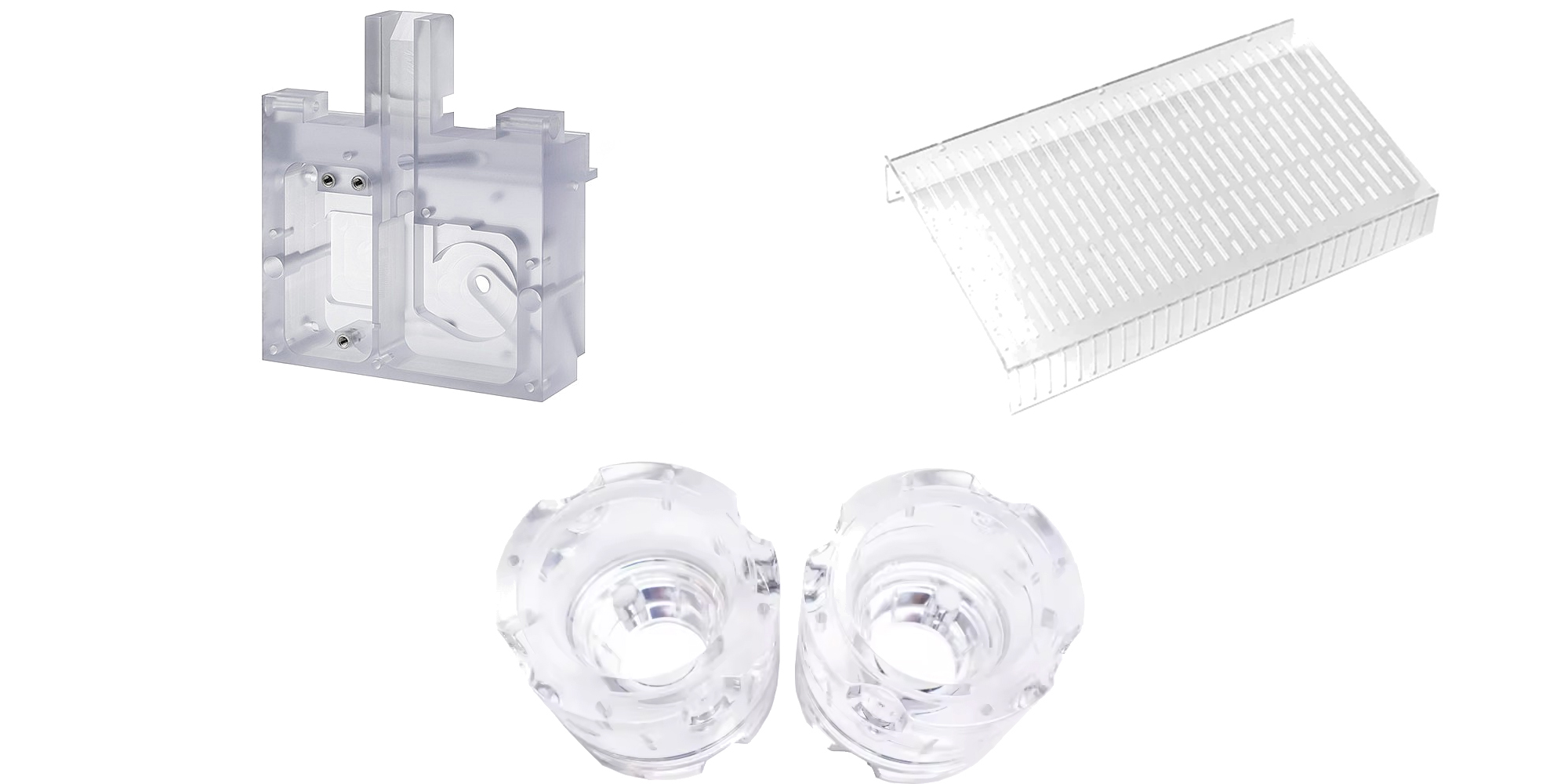
Advantages and Disadvantages of Polycarbonate Machining Parts
Advantages | Disadvantages |
---|---|
High Precision | Higher Cost for Large Volumes |
– Ensures parts meet strict specifications and tight tolerances. | – Less cost-effective than molding for high-volume production due to time-intensive nature. |
Smooth Finish | Material Waste |
– Achieves high-quality surface finishes essential for optical applications. | – Subtractive process results in significant material waste, impacting cost and environmental sustainability. |
Material Versatility | Design Limitations |
– Suitable for a wide range of applications, giving flexibility in design choices. | – Subtractive manufacturing restricts complexity compared to additive methods, which can create more intricate designs. |
Rapid Prototyping | Induced Stress and Micro-Cracks |
– Allows for fast iteration and optimization of designs, crucial in development environments. | – Machining can introduce stress and micro-cracks, potentially compromising part integrity. |
No Molds Needed | Potential Surface Imperfections |
– Reduces initial costs and setup times, ideal for prototyping and small batch production. | – May require additional finishing steps to remove blemishes or tool marks to meet design standards |
Polycarbonate CNC Machining Parts and Applications
Custom Delrin machining offers a vast array of possibilities for engineers and designers across various industries, providing them with unique benefits due to Delrin’s desirable material properties.
Chemical Properties of Polycarbonate
Polycarbonate’s unique properties are largely due to its robust backbone, which provides a balance of excellent toughness, high optical clarity, and good thermal resistance.
Property | Description |
---|---|
Basic Monomer | Bisphenol A (BPA) |
Linkage | Carbonate groups (–O–(C=O)–O–) link BPA units |
Chemical Formula | (C15H16O2)n, where n represents the number of repeating units |
Production Method | Typically produced by the reaction between BPA and phosgene, or by transesterification of BPA with diphenyl carbonate |
Impact Resistance | Extremely high, making it durable against impacts |
Optical Clarity | Excellent, allowing for clear visibility and light transmission |
Thermal Resistance | Good, can withstand higher temperatures without deforming |
Chemical Resistance | Resistant to oils, greases, and weak acids; sensitive to strong acids and bases |
Physical Properties of Polycarbonate Plastic
Polycarbonate is a favored engineering plastic, prized for its distinctive physical properties crucial across diverse technical disciplines. Here are 8 key properties that engineers and designers frequently evaluate:
Property | Value |
---|---|
Hardness (Rockwell) | M-70 to M-75 |
Tensile Strength | 9,000 psi (62 MPa) |
Impact Resistance | Extremely high |
Optical Clarity | 88% light transmission |
Thermal Stability | Up to 280°F (138°C) |
Coefficient of Thermal Expansion | 65 x 10^-6 per °C |
Flexural Modulus | 345,000 psi (2,379 MPa) |
Elongation at Break | 100-150% |
CNC Machining Processes for Polycarbonate
Both CNC turning and CNC milling not only utilize but also amplify the best qualities of polycarbonate, ensuring that each component is crafted to meet high standards of both functionality and aesthetic appeal.
CNC Turning
Ideal for crafting polished cylindrical parts, this process is particularly adept at producing components such as precision fittings and sleek casings that benefit from the material’s smooth finish and uniform diameter.
CNC Milling
This process is great for making detailed, three-dimensional parts. It’s used for things like custom light diffusers and strong, clear mechanical components.
Surface Finishes for Polycarbonate CNC machining
No, polycarbonate is not better than acrylic (PMMA) for machining.
Acrylic (PMMA) tends to be easier to machine than polycarbonate. It produces a smoother finish and is less prone to cracking or chipping during the machining process. PMMA also allows for a higher level of detail and can be polished to a high gloss finish more readily. On the other hand, polycarbonate, while tougher and more impact-resistant, can be more challenging to work with due to its higher toughness, which may require special handling to avoid damages during machining.