Custom PTFE Machining Tailored to Your Needs
Every project is unique, and our custom PTFE(Teflon) Machining is designed to match. Tell us your requirements, and we’ll adapt our techniques to produce PTFE parts that fit your exact needs in any industry, from aerospace to electronics.
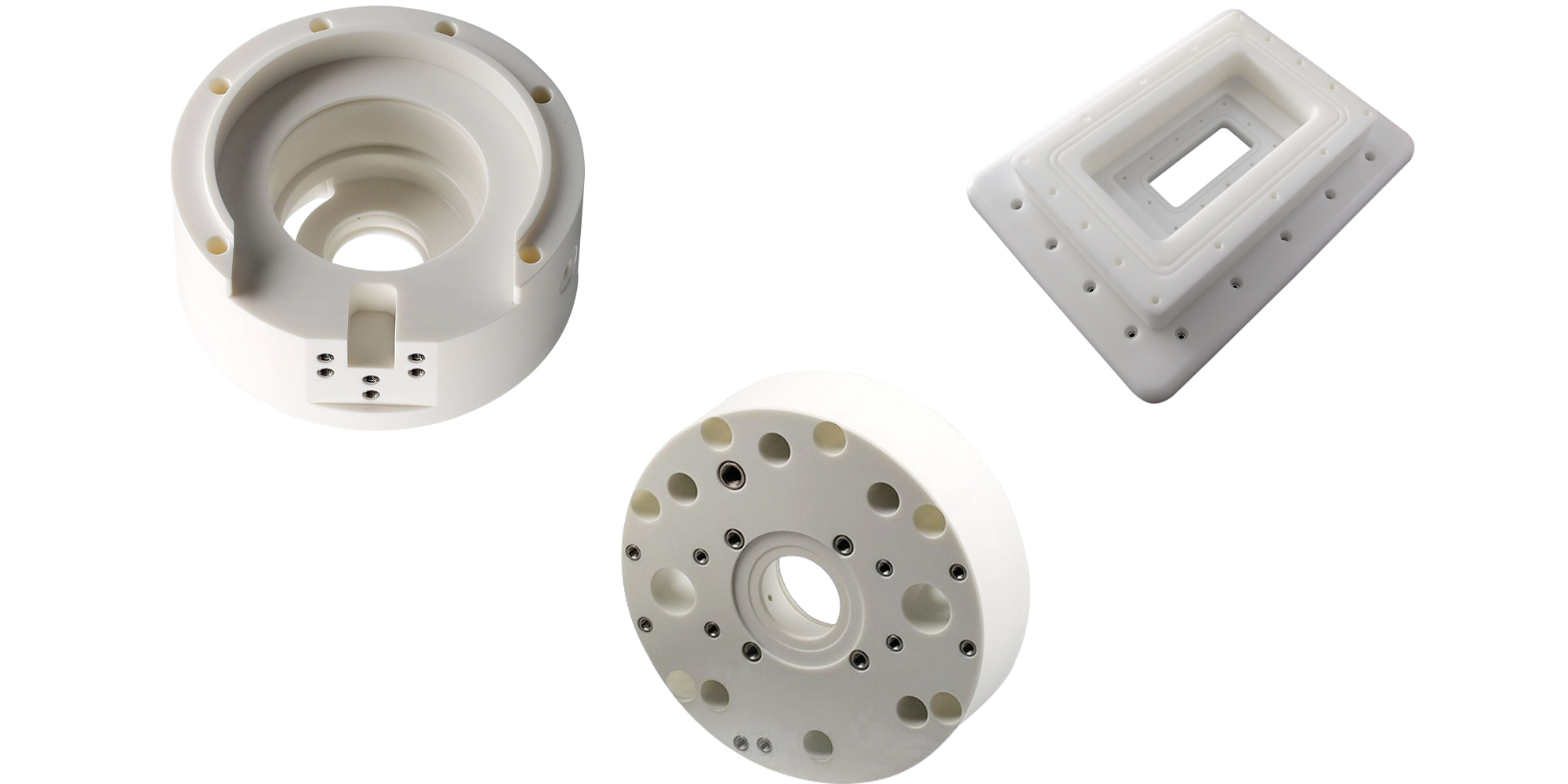
Upsides and Downsides of PTFE CNC Parts
Upsides | Downsides |
---|---|
Chemical Resistance | High Cost |
PTFE resists most chemicals, making it suitable for chemical processing. | PTFE is more expensive than many plastics. |
High Temperature Resistance | Difficult to Bond |
Withstands temperatures up to 260°C (500°F). | PTFE does not easily adhere to other materials. |
Low Friction | Creep and Deformation |
Has one of the lowest friction coefficients of any solid. | PTFE can deform under load over time. |
Non-Stick Surface | Poor Wear Resistance |
Useful in applications where materials must not stick. | Poor resistance to abrasion can limit its use. |
Electrical Insulation | Machining Challenges |
Excellent insulator across a wide range of frequencies and temperatures. | Difficult to machine precisely; requires specialized equipment. |
Biocompatibility | Sensitivity to UV Light |
Inert and non-toxic, suitable for medical applications. | PTFE can degrade when exposed to UV light, limiting outdoor applications. |
PTFE CNC Machining Parts and Applications
Polypropylene is a versatile thermoplastic widely used in precision CNC machining to produce various parts due to its favorable properties.
Aerospace Fuel Insulators
PTFE is very useful in aerospace because it can handle the harsh chemicals in rocket fuels and the extreme cold of space.
Automotive Bushings
PTFE is known for low friction. It is strong and doesn’t squash under pressure. This makes it perfect for cars that need to perform well, where both precision and toughness are key.
Custom Seals for Equipment
Beyond standard medical devices, PTFE’s bio-inertness enables its use in innovative biomedical applications like artificial limbs, where its lightweight and non-toxic nature contribute to its suitability for long-term human contact.
Artificial Limbs and Biomedical
PTFE is safe and light, which makes it good for making artificial limbs and other medical devices. It does not react with the body, so it’s safe for long-term use.
Specialized Gears in Robotics
PTFE is essential in robotics for crafting gears. These components operate seamlessly and make minimal noise, crucial for environments requiring precise movements and low sound levels.
Physical Properties of PTFE Material
PTFE (Polytetrafluoroethylene), often known by the brand name Teflon, possesses several distinctive physical properties that make it a valuable material across a wide range of applications. Here are some key physical properties of PTFE:
Property | Description |
---|---|
Yield Strength (Tensile) | Approximately 14-35 MPa depending on the grade and fillers used. |
Elongation at Break | 200-400%, showing high flexibility before breaking. |
Density | About 2200 kg/m³, indicating its relative heaviness among plastics. |
Hardness | Typically between 50-65 on the Shore D hardness scale. |
Chemical Resistance | Extremely resistant to most chemicals including acids, bases, and solvents. |
High Thermal Resistance | Operates up to 260°C (500°F) with a melting point of approximately 327°C (620.6°F). |
Low Friction | Very low coefficient of friction, beneficial for parts requiring minimal frictional resistance. |
Non-Stick Surface | Highly non-adhesive surface useful in food processing and other applications where cleanliness is crucial. |
Electrical Insulation | Excellent insulator over a broad range of frequencies and environmental conditions. |
Mechanical Properties | Maintains flexibility and stress resistance at high temperatures, suitable for cyclic loading. |
Dimensional Stability | Maintains precise dimensions under thermal stress, important for high-precision components. |
Creep Resistance | Good performance under long-term material load, important for applications requiring durability under stress. |
CNC Machining Process for PTFE
CNC machining of PTFE, involves several precise and carefully controlled steps due to the material’s unique properties. Here’s a detailed tips of the CNC machining process specifically tailored for PTFE:
Machining Aspect | Details |
---|---|
Tool Selection | Use sharp carbide or diamond-coated tools. Round PTFE cutting edges slightly to prevent cracks. Keep tools sharp. |
Speed and Feed Rates | Spindle speed: 250-600 RPM. Feed rate: 0.1-0.5 mm/rev. Fine finish: 200-500 fpm. Reduce feed for speeds above 500 fpm. |
Cooling and Heat Control | Avoid standard coolants. Use air blasts or non-reactive coolants. Effective at managing temperatures typically below 250°C. |
Support and Clamping | Use soft jaws or vacuum fixtures for secure, non-deforming hold. |
Drilling Operations | Secure PTFE well, use special drill bits. Move tool forward at 0.005-0.009 in/rev. Use in-out motion for heat management. |
Dimensional Stability | Monitor for dimensional changes due to low conductivity and high thermal expansion. Measure at controlled temperatures. |
General Machining Tips | Perform standard operations (turning, milling, drilling). Use coolant on lathes or for critical tolerances. |
CNC Turning and CNC Milling for PTFE Parts
Embrace Precision with tight tolerance ±0.01 mm: Experience swift and precise crafting of PTFE components for seamless applications.
PTFE is excellent for machining. Its low friction, high temperature resistance, and chemical inertness make it ideal for various applications. It can be machined using techniques like CNC turning and milling to create precise components for industries such as automotive and aerospace.