Reduce Costs and Improve Efficiency with ABS CNC Machining
Upgrade your machining strategies with advanced techniques specifically suited for ABS. Find out why ABS is the preferred material for various applications, from consumer electronics to automotive components.
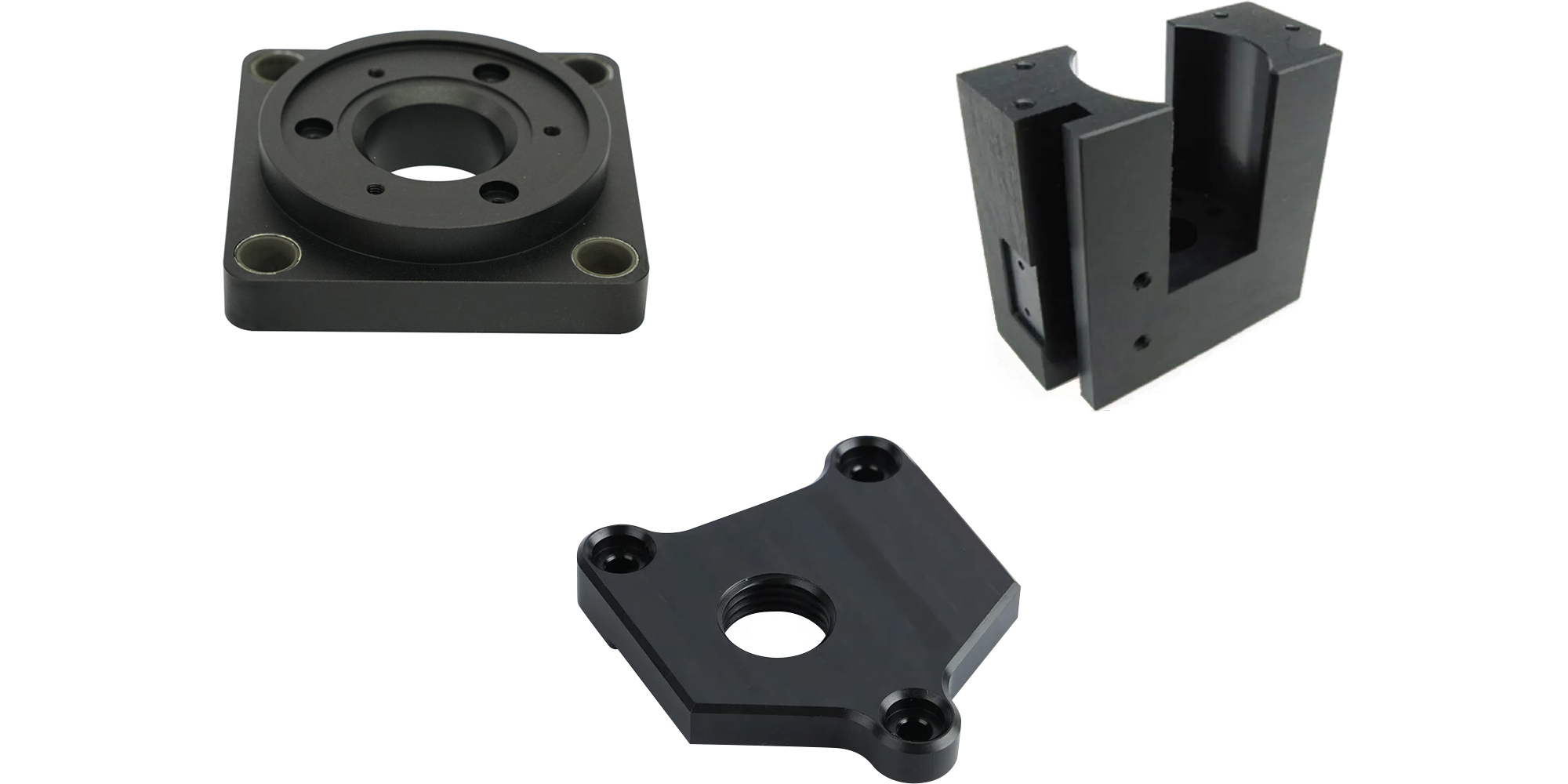
Strengths and Weaknesses of ABS Plastic
Machining Quote mechanical engineers have an in-depth understanding of the advantages and disadvantages of ABS materials. Customizing machining projects can be achieved with tolerances ±0.01 mm.
Strengths | Weaknesses |
---|---|
Impact resistant | Poor chemical resistance |
Durable | UV sensitive |
Thermally stable | Poor weatherability |
Easy to machine | Prone to warping |
Good electrical insulation | Not biodegradable |
Cost-effective | Produces smoke when burned |
ABS Precision Machining Parts and Applications
ABS plastic is a popular choice for precision machining parts due to its favorable properties. Here’s an overview of the typical parts and applications that utilize ABS precision machining:
Gears
Bearings
Electronic enclosures
Automotive interior components
Medical device housings
Toys
Luggage handles and components
Household appliance components
Fixtures
Jigs
Prototypes
Custom machinery components
Functional models
Decorative elements
Tooling components
Physical Properties of ABS Material
PTFE (Polytetrafluoroethylene), often known by the brand name Teflon, possesses several distinctive physical properties that make it a valuable material across a wide range of applications. Here are some key physical properties of PTFE:
Property | Value | Relevance |
---|---|---|
Density | 1.04 g/cm³ | Indicates the weight of ABS parts. |
Tensile Strength | 40-50 MPa | Measures resistance to being pulled apart. |
Flexural Strength | 60-80 MPa | Indicates the material’s ability to resist deformation under load. |
Impact Strength | 15-30 kJ/m² | Shows resistance to sudden impacts. |
Thermal Expansion | 80 µm/m°C | Useful for understanding how the material will expand or contract with temperature changes. |
Heat Deflection Temperature | 88°C at 1.8 MPa | Critical for applications involving heat exposure. |
Melting Point | 105°C | Important for processing and high-temperature applications. |
Glass Transition Temperature | 105°C | Critical for understanding at what temperature the material will start to soften. |
CNC Machining Process for PTFE
Machining ABS plastic effectively requires understanding its properties and how to optimize the manufacturing process for this material. Here are six practical tips for machining ABS plastic by Machining Quote. This is also the best practice to avoid warping in ABS machining.
Tip | Tool Type | Cutting Speed | Power/Feed Rate | Description |
---|---|---|---|---|
Use Sharp Tools | Carbide end mills | N/A | N/A | Sharp, high-quality carbide tools prevent melting and ensure clean cuts. |
Optimize Cutting Speed | HSS (High Speed Steel) drills | 100-150 m/min | Feed rate: 0.05-0.20 mm/rev | Balance speed to avoid melting and chipping, optimizing the efficiency. |
Apply Cooling Techniques | Any applicable tool | N/A | N/A | Use coolants or compressed air to prevent heat buildup and improve finish. |
Secure Clamping | Any applicable tool | N/A | N/A | Ensure secure clamping to avoid movement without deforming the ABS. |
Gradual Material Removal | Carbide milling tools | 200-300 m/min | Depth of cut: 1-3 mm per pass | Remove material in smaller increments to manage heat and reduce stress on the plastic. |
Maintain Controlled Environment | Any applicable tool | N/A | N/A | Keep the machining environment controlled to prevent ABS from warping due to temperature fluctuations. |
CNC Turning and CNC Milling for ABS Parts
Both CNC turning and milling are effective for machining ABS due to the material’s good machinability and stability.
ABS can be used for applications that require moderate heat resistance. However, it’s important to consider its glass transition temperature of about 105°C, beyond which it may soften.