Custom CNC Milling Services in China
Looking for Custom CNC Milling Services in China manufacturer? Our facilities are equipped with the latest CNC machinery, capable of handling diverse materials from metals to plastics.
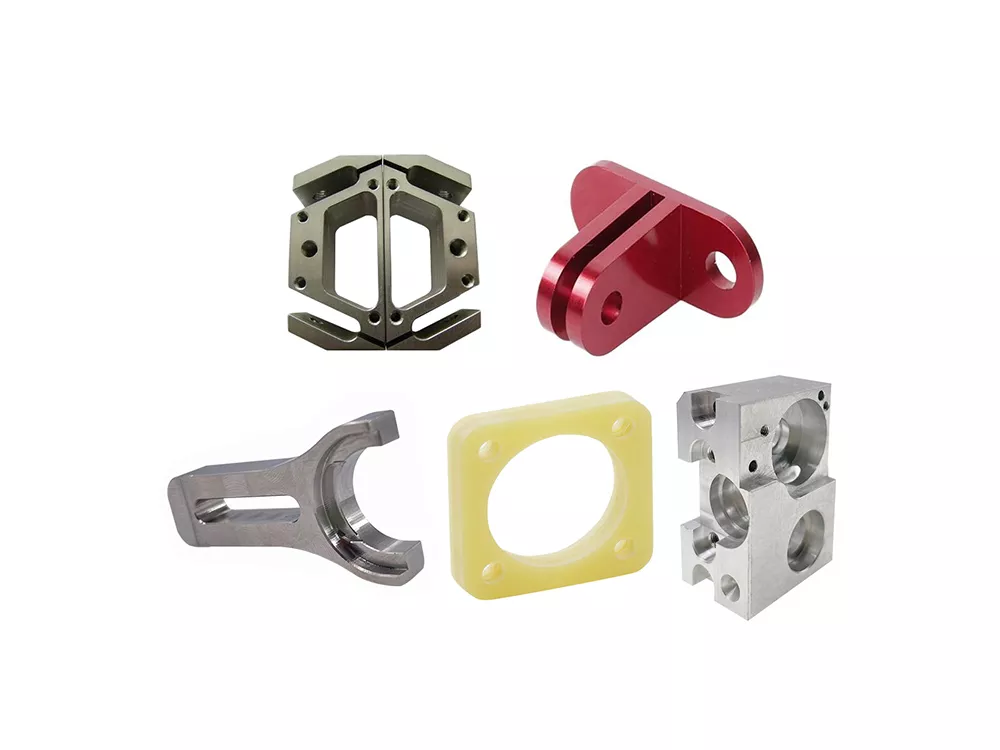
Advantages of Online CNC Milling Services China
CNC milling services in China can offer a compelling combination of cost efficiency, quality, speed, and flexibility, making them an excellent choice for businesses looking to optimize their manufacturing processes.
Advantage | Description |
---|---|
Cost Efficiency | One of the most prominent advantages of using CNC milling services in China is cost-effectiveness. Our best engineers can save you material and design costs. |
High Quality and Precision | Despite the lower costs, quality is not compromised. Our CNC milling tolerance is +/- 0.01mm. |
Scalability and Flexibility | Chinese CNC milling providers are well-equipped to handle both large-scale production and small, customized projects. |
Rapid Turnaround Times | The combination of efficient workflows, 24/7 production capabilities, and excellent logistical frameworks ensures that projects can be completed quickly and delivered on time. |
Advanced Technology Integration | Using the latest 3-Axis to 5-Axis CNC Milling Machines. |
Comprehensive Service Offerings | From design and prototyping to final production and post-processing, MachiningQuote provides a one-stop service. |
Strong Supply Chain and Logistics | Machining Quote has a robust supply chain and advanced logistics capabilities. |
Custom CNC Milling Parts and Used
Custom CNC milling allows for the creation of highly specific and tailored parts, making it a vital tool in product development and manufacturing across these sectors.
Case Studies Of CNC Milling Services
These case studies illustrate how Machining Quote’s CNC milling services are successfully applied across various industries, delivering high-quality, precision-machined parts that enhance product performance and operational efficiencies.
Custom CNC Milling Materials
Aluminum
Aluminum is a lightweight, corrosion-resistant metal ideal for applications requiring a high strength-to-weight ratio and good thermal conductivity. It’s easy to machine and extensively used in aerospace, automotive, and consumer electronics. Common types of aluminum alloys like 6061 and 7075 offer enhanced mechanical properties, such as improved toughness and hardness.
- Price: $$
- Lead Time: 10 days
- Wall Thickness: 0.75 mm
- Tolerances:+/-0.125mm (±0.005″)
- Max part size: 200 x 80 x 100 cm
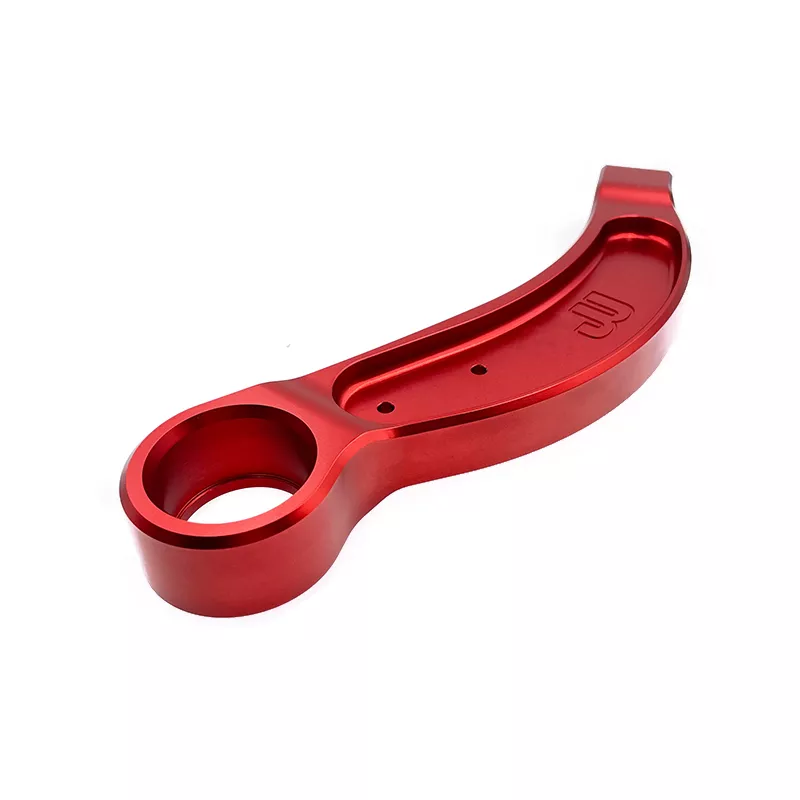
Copper
Copper is highly conductive to both heat and electricity, making it popular in electrical applications, heat exchangers, and automotive parts. It is relatively easy to machine and provides a unique combination of ductility, strength, and thermal conductivity. Its natural resistance to corrosion and aesthetic appeal also make it a choice material for decorative applications.
- Price: $$$
- Lead Time: =10 days
- Wall Thickness: 0.75 mm
- Tolerances: plusmn;0.125mm (±0.005″)
- Max part size: 200 x 80 x 100 cm
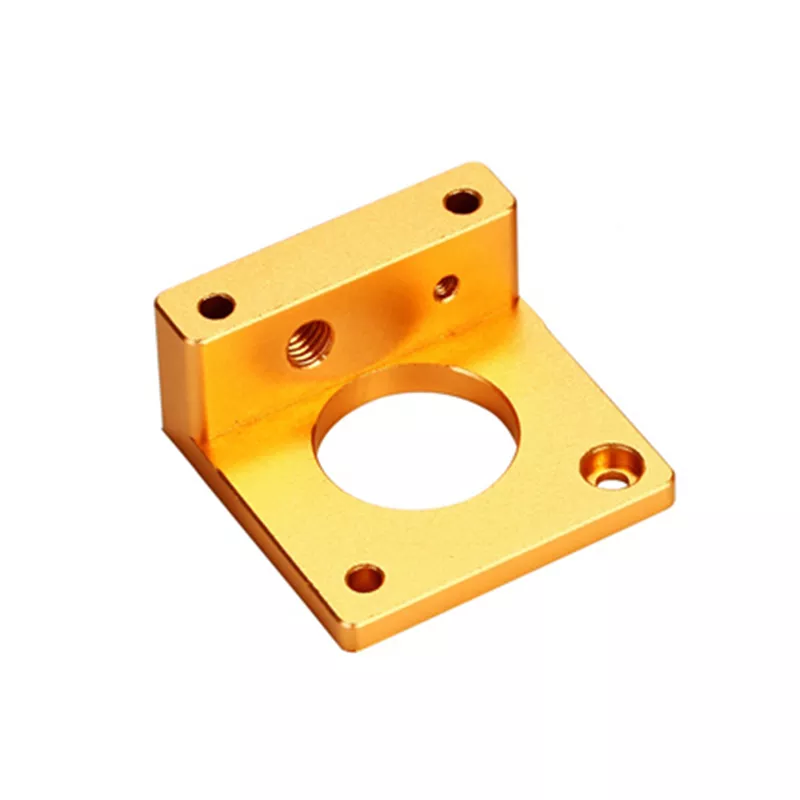
Brass
Brass is an alloy of copper and zinc, known for its machinability and corrosion resistance. It’s often used for decorative items, plumbing fixtures, electrical components, and musical instruments. Brass provides a balance between strength and ductility and can be easily machined into complex shapes.
- Price: $$$
- Lead Time: < 10 days
- Wall Thickness: 0.75 mm
- Tolerances: ±0.125mm (±0.005″)
- Max part size: 200 x 80 x 100 cm
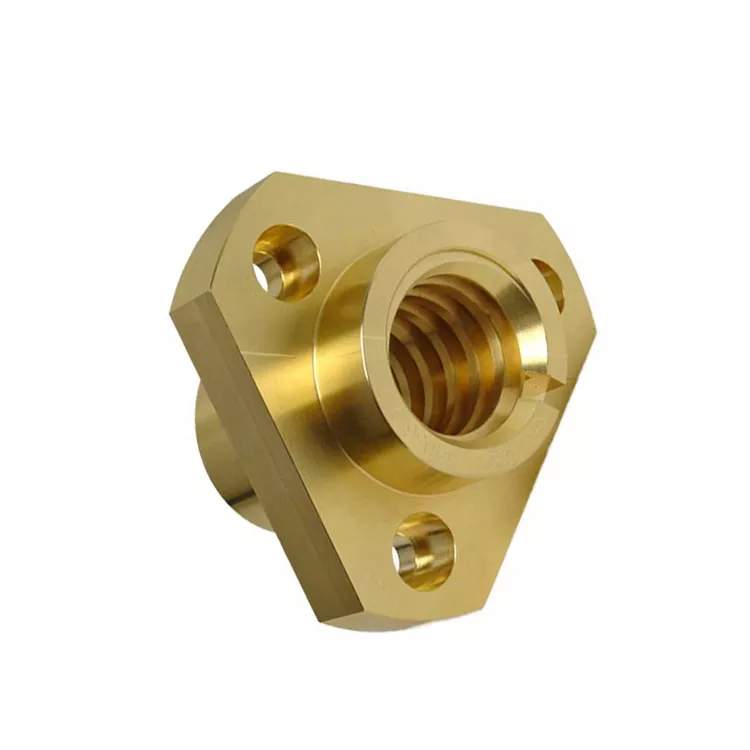
Stainless Steel
Stainless Steel is renowned for its corrosion resistance and strength. It’s widely used in food processing equipment, medical devices, and general metal fabrication. Stainless steel alloys, like 304 and 316, offer a good balance of corrosion resistance, machinability, and cost-effectiveness. It’s a versatile material suitable for a wide range of applications.
- ?Price: $$
- ?Lead Time: < 10 days
- ?Wall Thickness: 0.75 mm
- ?Tolerances: ±0.125mm (±0.005″)
- ?Max part size:200 x 80 x 100 cm
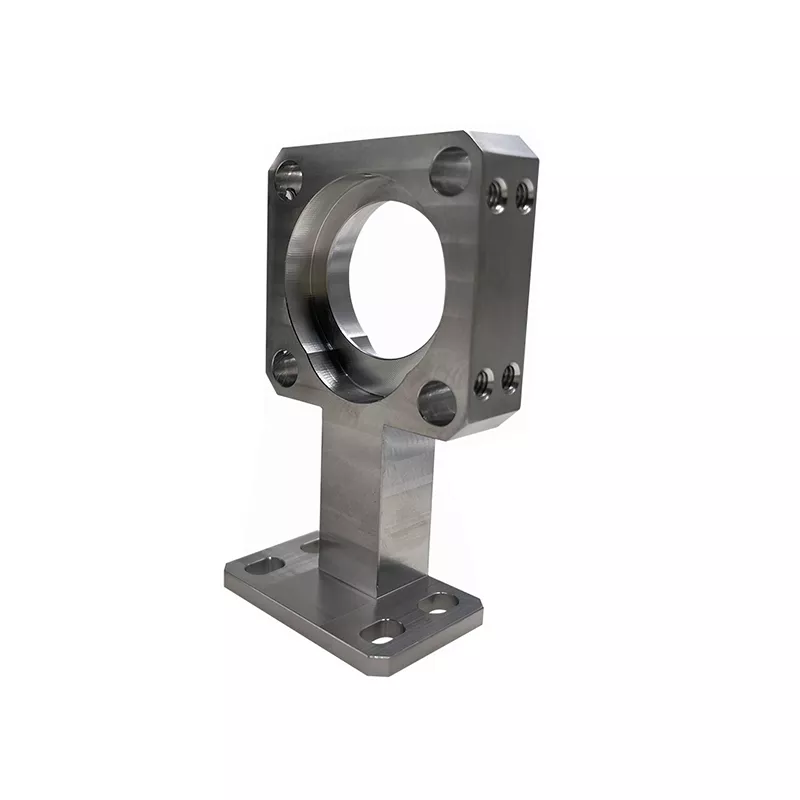
Titanium
Titanium is known for its exceptional strength, lightweight, and high corrosion resistance. It’s often used in aerospace, medical implants, and high-performance automotive applications. Titanium is challenging to machine but offers superior mechanical properties and a very high strength-to-weight ratio, making it ideal for advanced engineering applications.
- Price: $$$$$
- Lead Time: < 10 days
- Wall Thickness: 0.75 mm
- Tolerances: ±0.125mm (±0.005″)
- Max part size: 200 x 80 x 100 cm
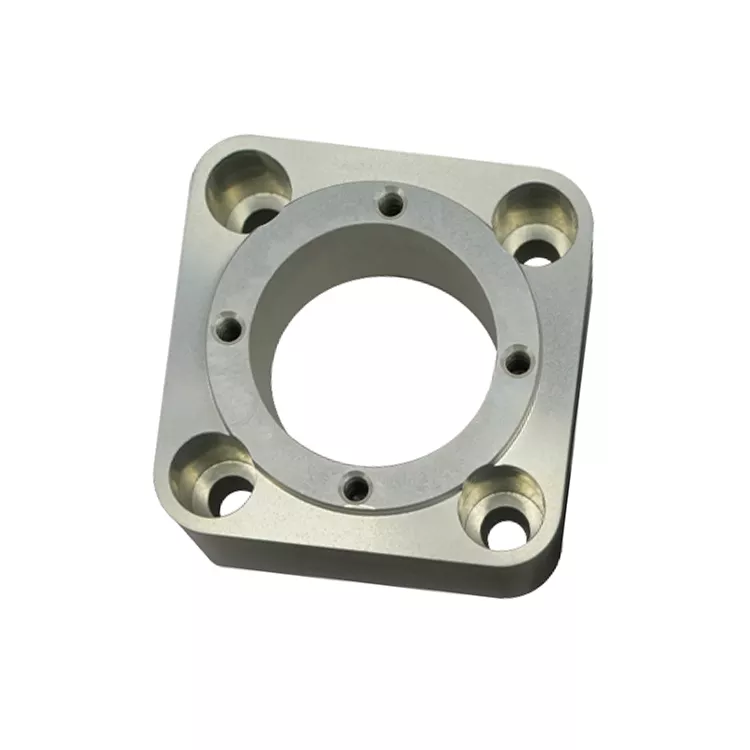
Plastics
Plastics in CNC machining offer versatility and a wide range of mechanical properties. Common plastics like ABS, Nylon, and Polycarbonate are lightweight, corrosion-resistant, and offer varying degrees of strength and flexibility. Plastics are used in applications from consumer products to automotive components, where complex shapes and low production costs are priorities.
- POM
- Nylon
- ABS
- PEEK
- PTFE
- PC
- HDPE
- PVC
- PMMA
- PET
- PP
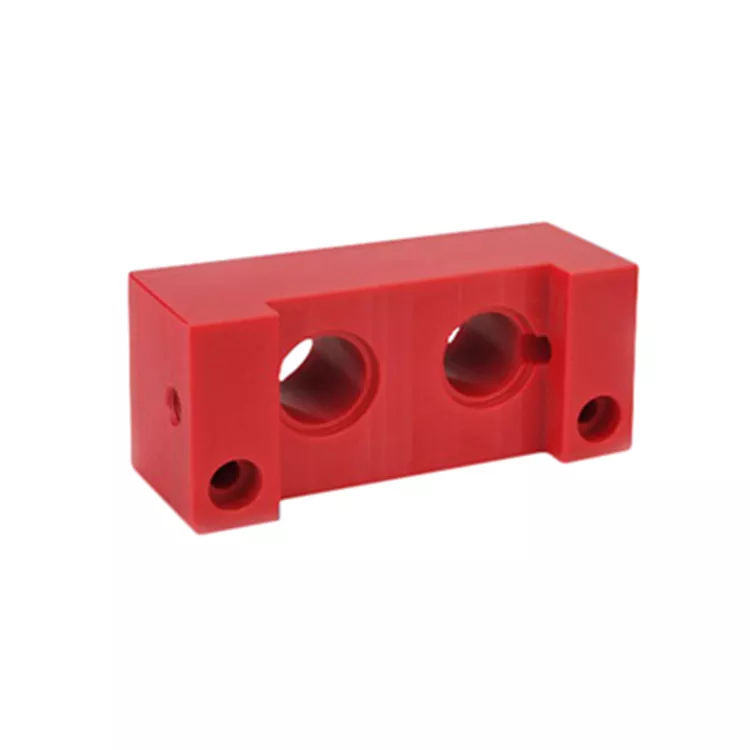
Technical Capabilities and Specifications of CNC Milling Service
This table provides a comprehensive overview of the technical capabilities relevant to those needing CNC milling services, such as the maximum part dimensions, tooling details, material compatibility, and other advanced features.
Specification | Details | Note |
---|---|---|
Maximum Part Dimensions | 100” x 50” x 40” (2540 x 1270 x 1016 mm) | Capacity may vary depending on CNC milling center specifications. |
Axis Control | Up to 5-axis CNC control | Enables complex geometries and reduces setup times. |
Spindle Speed | Up to 12000 RPM | Higher speeds possible for advanced materials and fine detailing. |
Tolerances | Typical Precision: +/- 0.0005 inches (0.0127 mm) | Tighter tolerances achievable based on material and part complexity. |
Surface Finish | As low as 8 microinch Ra | Finer finishes can be achieved with additional processes like chemical milling. |
Tool Magazine Capacity | Varies, e.g., 40+ tools | Larger capacity allows for versatile operations without manual tool changes. |
Feed Rate | Up to 1000 inches per minute | Critical for efficiency in large scale and complex part machining. |
Material Compatibility | Metals, Plastics, Composites, and more | CNC machines can handle a diverse range of materials. |
Certifications | ISO 9001:2015, AS9100, ISO 13485 | Ensures compliance with quality, aerospace, medical, and environmental standards. |
Automated Features | Automatic Tool Changers, Probing Systems | Enhances productivity and precision in complex production runs. |
Control System | Advanced CNC Controllers | Supports complex programming and real-time adjustments for high precision. |
Post Processing Services for CNC Milling Parts
Post-processing services for CNC milling parts are essential steps taken after the initial machining. These steps enhance the part's function, appearance, and performance. They range from simple cleaning and inspection to more complex treatments that improve the material properties or ready the parts for their final use.