Types of Surface Finishing for CNC Parts
We not only provide custom CNC machining services, but also post-processing of parts, such as common surface finishes. There is always one that can meet your needs.
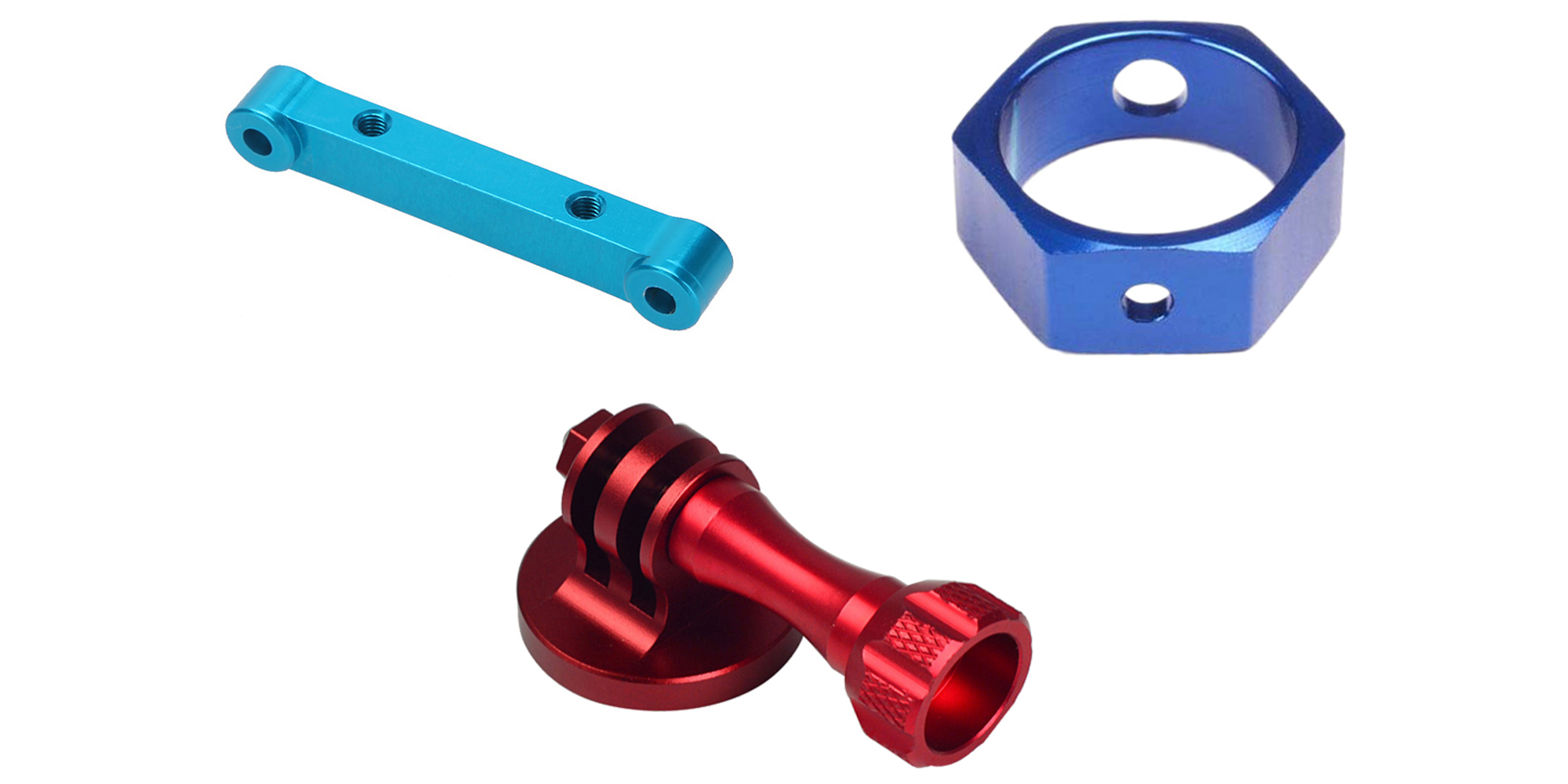
Why CNC Parts need Surface Finishing Services
Finishing manufacturing process is a crucial step in the manufacturing of CNC parts to meet the specific requirements of different applications, ensuring durability, functionality, and compatibility with other components.
Common Surface Finishing Processes
Surface treatment is an important processing method for CNC machined parts, which aims to optimize its surface characteristics through different technical means to adapt to various use environments and performance requirements.
Anodizing
This electrochemical process creates an oxide layer on metal surfaces, typically aluminum, enhancing corrosion resistance and allowing for coloration through dyeing.
Powder Coating
This technique involves spraying a fine powder onto the part and then curing it under heat to form a tough layer. It increases durability and offers a wide range of color choices.
Electroplating
This involves depositing a metal or another substance onto the part using an electrical current, enhancing properties like corrosion resistance, hardness, and conductivity. Common coatings include nickel, chrome, and zinc.
Passivation
Specifically useful for stainless steel, this chemical process removes free iron from the surface, bolstering the naturally corrosion-resistant chromium oxide layer.
Bead Blasting
By blasting small glass beads at high pressure onto the surface, this method achieves a uniform matte finish that reduces light reflection and enhances texture.
Polishing
This process uses abrasives or polishing discs to remove surface irregularities, achieving a mirror-like smooth finish that significantly enhances appearance.
Brushing
This technique creates a unidirectional satin finish by using brushes or similar tools, which adds visual depth and can hide minor scratches.
Black Oxide
Used primarily for ferrous metals, this chemical conversion creates a black oxide layer that improves appearance and offers mild corrosion resistance.
Chemical Film/Chromate Conversion Coating
This treatment provides a corrosion-resistant layer on metals like aluminum, serving also as a primer for additional coatings.
Laser Engraving
While mainly used for marking, it can also alter surface texture and appearance for decorative purposes.
Examples of Surface Finishes
Not sure which surface finish is right for you? Contact us for a personalized consultation and expert advice tailored to your specific requirements.
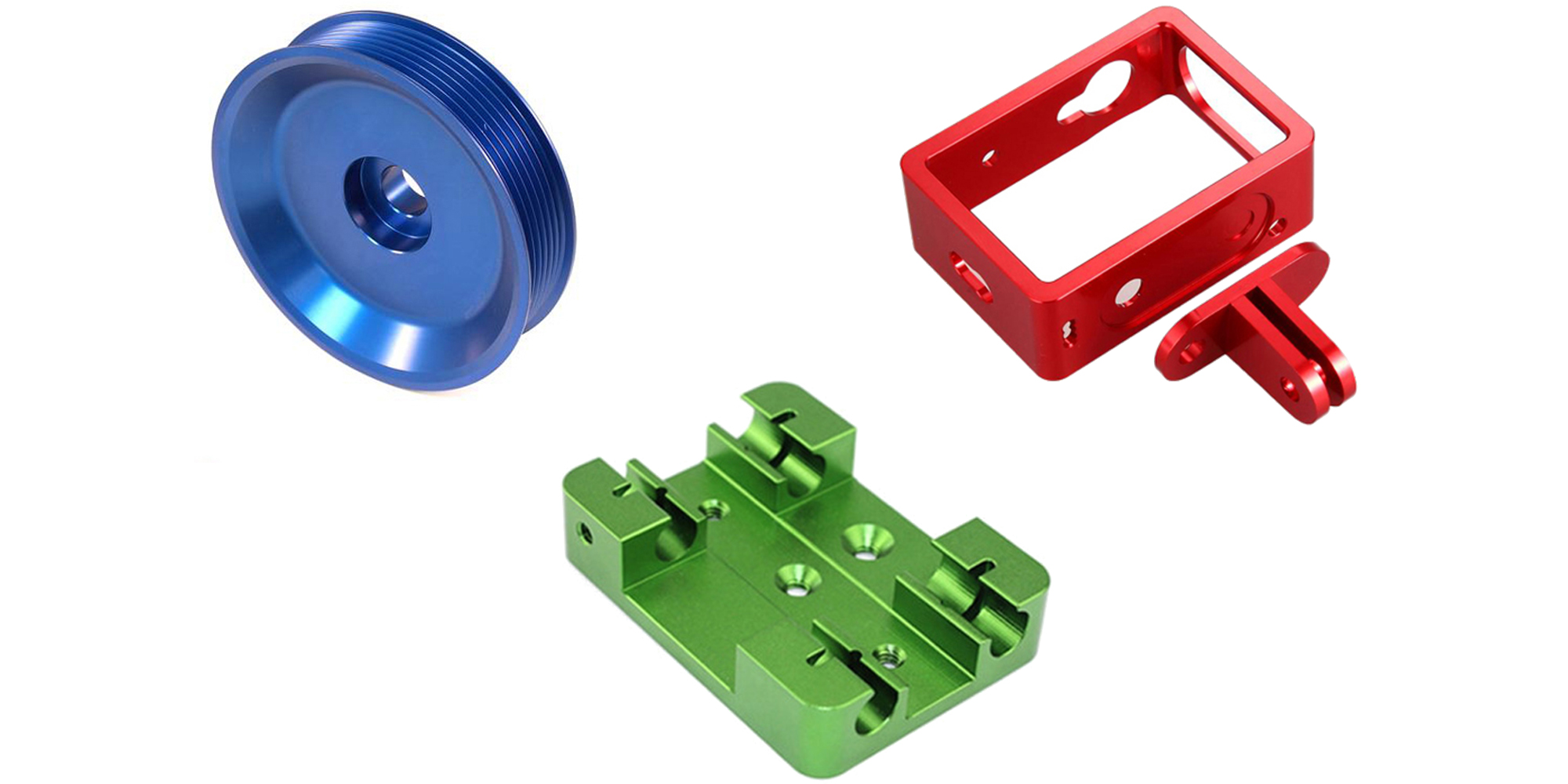
5 Factors to Consider When Selecting Surface Finishing
By carefully evaluating these factors, you can make informed decisions about the most suitable surface finishing technique for their CNC machined parts, ensuring optimal performance, durability, and cost-effectiveness.
Factor | Description |
---|---|
Performance Requirements | Evaluate the necessary characteristics such as wear resistance, corrosion resistance, and conductivity. These depend on the function of the part. |
Material of the Part | Choose a finishing process compatible with the material of the part to ensure effectiveness and prevent damage. For example, anodizing is good for aluminum but unsuitable for most steels. |
Aesthetic Considerations | Consider the desired visual outcome, including color, texture, and gloss, especially for consumer-facing parts. Different finishes can enhance the product’s appearance. |
Environmental Exposure | Assess the environmental conditions the part will be subjected to, such as chemicals, temperature extremes, or physical wear. Select a finish that can protect the part under these conditions. |
Cost and Process Efficiency | Factor in the cost of different finishing processes and their impact on the manufacturing timeline. Balancing these with the quality and performance benefits is crucial for a cost-effective process. |