Table of Contents
- Introduction
- Properties Comparison: PE and PTFE in Plastic Machining
- Machining Techniques for PE and PTFE Plastics
- Design Considerations for PE and PTFE Components
- Cost Analysis: PE vs PTFE Machining
- Applications of PE and PTFE in Engineering and Design
- Surface Finishing Options for PE and PTFE
- Challenges in Machining PE and PTFE Plastics
- Future Trends in PE and PTFE Plastic Machining
- Conclusion
Introduction
Polyethylene (PE) and Polytetrafluoroethylene (PTFE) are widely used in various industries due to their unique properties. PE is known for its strength, durability, and flexibility. PTFE is renowned for its high melting point, excellent chemical resistance, and outstanding thermal properties. Machining these materials requires specialized knowledge and techniques. This guide provides engineers and designers with insights into machining PE and PTFE plastics, ensuring optimal performance and efficiency.
Properties Comparison: PE and PTFE in Plastic Machining
PE Properties
- High ductility and impact resistance
- Types: HDPE (high strength) and LDPE (flexibility)
- Uses: Packaging, outdoor applications, containers
PTFE Properties
- High chemical resistance
- Temperature range: -200°C to +260°C
- Non-stick properties
- Uses: Chemical processing, high-purity applications, sliding surfaces
Machinability Comparison
- PE: Easier to machine, less costly, shorter production time
- PTFE: Requires specialized equipment, higher production cost, superior performance in harsh environments
Machining Techniques for PE and PTFE Plastics
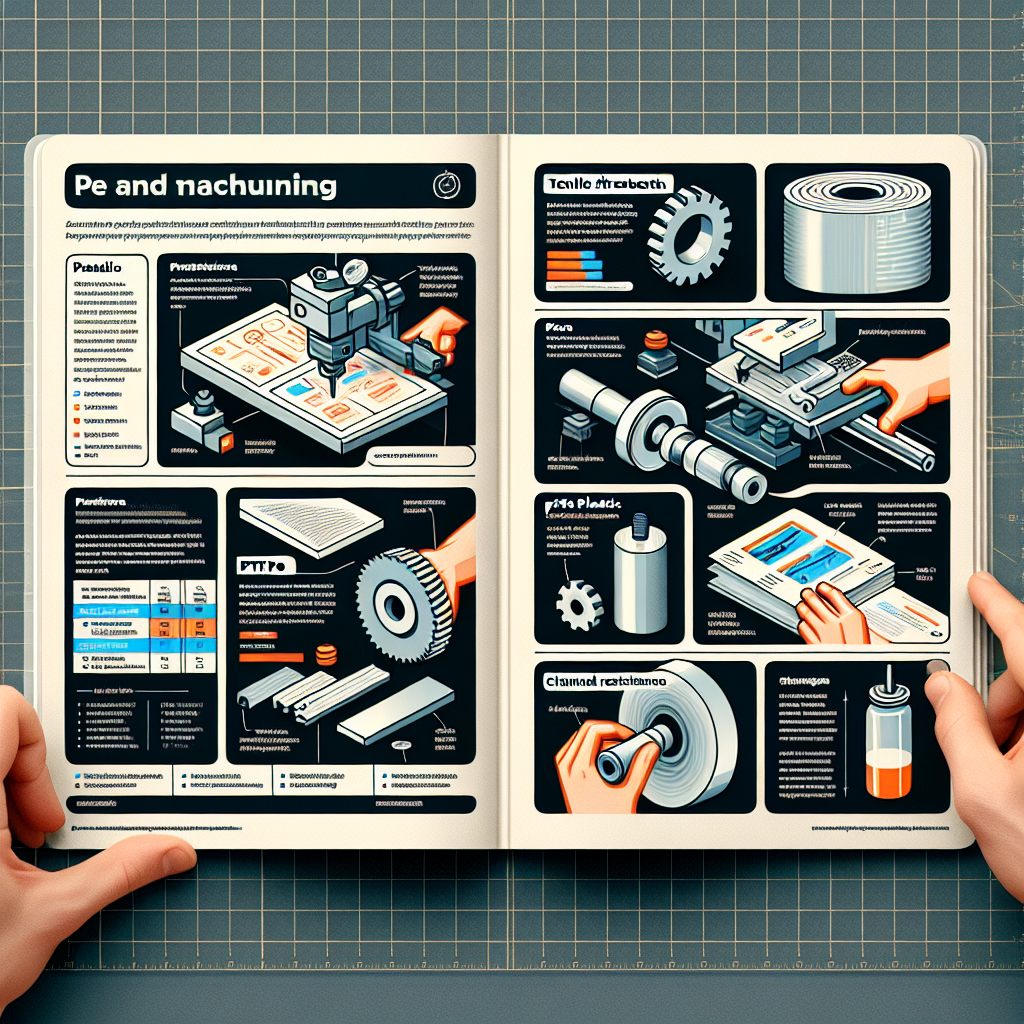
PE Machining
- Challenges: Softness, material deformation
- Techniques: Sharp, single-point tools; high spindle speed; moderate feed rate
PTFE Machining
- Challenges: Toughness, high melting point
- Techniques: Sharp, polished tools; intermittent cutting; minimal cooling
CNC Machining
- Benefits: Enhanced precision, consistent quality, reduced human error
Coolants
- PE and PTFE: Prefer dry machining or minimal air blast to avoid thermal expansion and warping
Post-Machining
- Burrs and Surface Irregularities: May require flame polishing or other methods to achieve desired surface quality
Design Considerations for PE and PTFE Components
Material Characteristics
- PE: High impact resistance, flexibility, chemical stability
- PTFE: Outstanding chemical resistance, high temperature tolerance, low friction
Mechanical Properties
- PE: Significant deformation before failure
- PTFE: Higher resistance to heat, prone to creep
Thermal Properties
- PE: Significant expansion/contraction with temperature changes
- PTFE: High thermal expansion coefficient, requires allowances for expansion in design
Machining
- PE: Sharp, single-point tooling, support for material
- PTFE: Appropriate tooling speeds and feeds, precise control to avoid smearing
Environmental Impact
- PE and PTFE: Proper management of chips and dust, consider environmental footprint
Cost Analysis: PE vs PTFE Machining
PE Cost Factors
- Lower raw material cost
- Straightforward machining process
- Less abrasive on machinery
PTFE Cost Factors
- Higher raw material cost
- Specialized tools and slower machining speeds
- Higher tool wear
Long-Term Benefits
- PE: Cost-effective for general applications
- PTFE: Economical for specialized applications requiring unique properties
Environmental Impact
- PE: Recyclable, but has associated costs
- PTFE: Less straightforward to recycle, higher disposal costs
Applications of PE and PTFE in Engineering and Design
PE Applications
- Packaging: Plastic bottles, films, containers
- Construction: Corrosion-resistant piping, geomembranes, plastic lumber
PTFE Applications
- Aerospace: Heat shields, wire insulation, slide bearings
- Electronics: Insulator cables, connector assemblies
- Industrial: Gears, bearings, chemical processing equipment
Surface Finishing Options for PE and PTFE
PE Surface Finishing
- Flame polishing for glossy finish
- Buffing for smooth surfaces
- Chemical treatments for enhanced properties
PTFE Surface Finishing
- Etching for better adhesive properties
- Mechanical abrasion for surface roughness
- Coatings for improved color, scratch resistance, and UV stability
Challenges in Machining PE and PTFE Plastics
Material Deformation
- PE and PTFE: Softness can lead to deformation during machining
- Use specialized tooling and techniques to minimize distortion
Thermal Properties
- PE and PTFE: Low thermal conductivity can cause melting or burning
- Use effective cooling strategies to prevent overheating
Tool Wear
- PE and PTFE: High tool wear due to abrasive nature
- Select appropriate tool materials and consider tool wear in planning</ li>
Swarf and Chip Management
- PE and PTFE: Manage chips and swarf properly to minimize environmental impact
Future Trends in PE and PTFE Plastic Machining
Automation and Robotics
- Increased production rates and precision
- Reduced human error
Specialized Machining Tools
- Tools optimized for PE and PTFE properties
- Diamond-coated tools and ultra-hard materials
Digitalization and Industry 4.0
- Advanced CNC systems for better control
- Digital modeling and simulation tools
Environmental Sustainability
- Recycling of plastic waste
- Use of greener machining fluids
- Development of biodegradable alternatives
Conclusion
When choosing between PE and PTFE for plastic machining services, engineers and designers must consider the unique properties and applications of each material. PE offers excellent impact resistance, flexibility, and cost-effectiveness, making it suitable for a wide range of general applications. In contrast, PTFE stands out for its superior chemical resistance, high-temperature tolerance, and low friction, which are ideal for specialized applications in chemical handling, electronics, and aerospace industries. The decision should be based on the specific requirements of the project, including mechanical stresses, environmental conditions, and budget constraints. Understanding the distinct advantages of each material will enable engineers and designers to select the most appropriate plastic for their machining needs, ensuring optimal performance and durability of the final product.