Stainless Steel 301 vs 440: A Comprehensive Guide
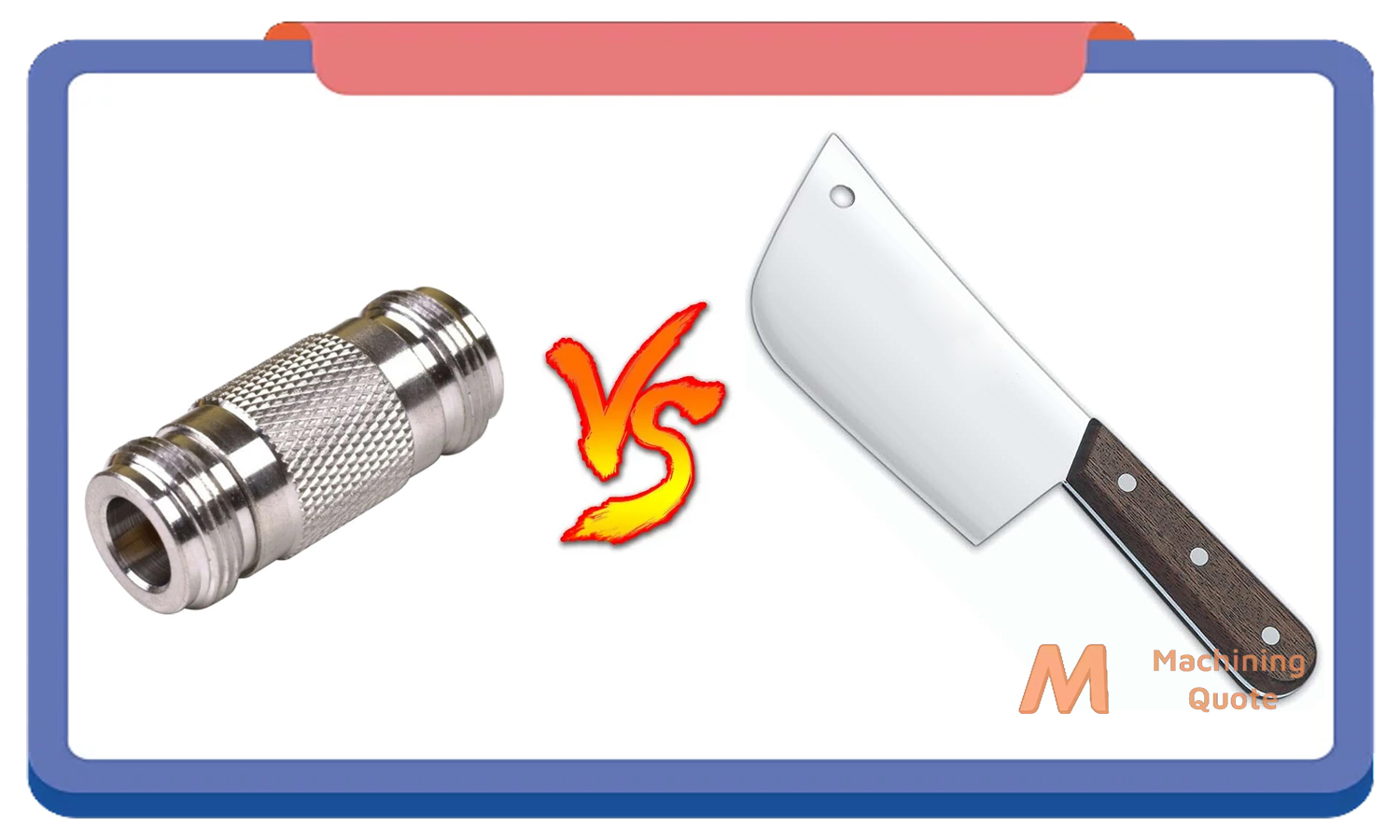
Introduction
When it comes to selecting the right stainless steel for your project, understanding the differences between various grades is crucial. In the world of manufacturing and mechanical design, two commonly used grades are Stainless Steel 301 and Stainless Steel 440. Each has unique properties that make them suitable for specific applications. In this comprehensive guide, we will delve into the properties, applications, advantages, and disadvantages of Stainless Steel 301 and 440 to help you make an informed decision.
What is Stainless Steel 301?
Stainless Steel 301 is an austenitic stainless steel known for its high strength and excellent corrosion resistance. It is a versatile material widely used in the automotive, aerospace, and manufacturing industries.
Chemical Composition
Element | Content (%) |
---|---|
Chromium | 16-18 |
Nickel | 6-8 |
Carbon | 0.15 max |
Manganese | 2.00 max |
Silicon | 1.00 max |
Phosphorus | 0.045 max |
Sulfur | 0.030 max |
Properties
Mechanical Properties
Property | Value |
---|---|
Tensile Strength | 930 MPa (135,000 psi) |
Yield Strength | 520 MPa (75,000 psi) |
Elongation at Break | 40% |
Hardness (Rockwell B) | 95 max |
Physical Properties
Property | Value |
---|---|
Density | 7.93 g/cm³ |
Melting Point | 1425-1510°C |
Specific Heat | 0.500 J/g-°C |
Thermal Conductivity | 16.3 W/m-K |
Applications
Stainless Steel 301 is widely used in applications that require high strength and good ductility. Some common applications include:
- Automotive trim
- Aircraft components
- Conveyor belts
- Architectural structures
- Springs and fasteners
What is Stainless Steel 440?
Stainless Steel 440 is a high-carbon martensitic stainless steel. It is well-known for its high hardness and wear resistance, making it ideal for applications that require excellent edge retention and durability.
Chemical Composition
Element th> | Content (%) |
---|---|
Chromium | 16-18 |
Carbon | 0.95-1.20 |
Manganese | 1.00 max |
Silicon | 1.00 max |
Phosphorus | 0.040 max |
Sulfur | 0.030 max |
Molybdenum | 0.75 max |
Properties
Mechanical Properties
Property | Value |
---|---|
Tensile Strength | 760-1970 MPa (110,000-285,000 psi) |
Yield Strength | 450-1900 MPa (65,000-275,000 psi) |
Elongation at Break | 2-20% |
Hardness (Rockwell C) | 58-62 |
Physical Properties
Property | Value |
---|---|
Density | 7.75 g/cm³ |
Melting Point | 1480-1530°C |
Specific Heat | 0.460 J/g-°C |
Thermal Conductivity | 24.2 W/m-K |
Applications
Stainless Steel 440 is frequently utilized in applications where high hardness and wear resistance are paramount. Common applications include:
- Cutlery (knives and scissors)
- Valve components
- Bearings
- Surgical instruments
- High-grade machine parts
Comparing Stainless Steel 301 and 440
Corrosion Resistance
Stainless Steel 301 offers good corrosion resistance, particularly in mild environments. However, it may not perform as well in more aggressive environments or when exposed to chlorides and acids. On the other hand, Stainless Steel 440, although more prone to corrosion than 301, can offer satisfactory resistance in environments where its superior hardness and wear resistance are required.
Strength and Hardness
Stainless Steel 301 is known for its high tensile and yield strength, which makes it suitable for applications requiring good strength-to-weight ratios. However, Stainless Steel 440 stands out with its superior hardness and edge retention capabilities, making it ideal for cutting tools and wear-resistant applications.
Ductility and Formability
Stainless Steel 301 exhibits excellent ductility and formability, making it easy to work with in various fabrication processes such as bending, stretching, and deep drawing. Conversely, Stainless Steel 440, due to its high carbon content and martensitic structure, is less ductile and more challenging to form and machine.
Cost and Availability
Both Stainless Steel 301 and 440 are widely available, but their costs can vary significantly. Generally, Stainless Steel 440 is more expensive due to its higher carbon content and specialized heat treatment processes required to achieve its superior hardness.
Practical Considerations in Selection
Application-Specific Requirements
When choosing between Stainless Steel 301 and 440, it is essential to consider the specific requirements of your application:
- For applications requiring high strength and ductility, such as springs, automotive components, and architectural structures, Stainless Steel 301 is an excellent choice.
- For applications needing high hardness and wear resistance, such as cutting tools, bearings, and surgical instruments, Stainless Steel 440 is more suitable.
Environmental Factors
The operating environment plays a critical role in material selection. If your application is exposed to corrosive environments, consider the level of corrosion resistance required. While neither grade offers the corrosion resistance of grades like 304 or 316, 301 may perform better in less aggressive environments.
Fabrication and Processing
Consider the ease of fabrication and processing. Stainless Steel 301’s excellent formability can simplify manufacturing processes, reduce costs, and improve production efficiency. However, if the application demands high precision and durability, the added difficulty in processing Stainless Steel 440 may be justified.
Expert Opinions and Testimonials
Industry Experts
John Smith, a senior metallurgist at Tuofa, notes:
“Stainless Steel 301’s balance of strength and ductility makes it a go-to material in many high-stress applications. In contrast, Stainless Steel 440’s exceptional hardness and wear resistance make it indispensable in the tool and cutlery industry.”
Customer Testimonials
Anna Liu, a mechanical engineer at a major aerospace company:
“We rely on Stainless Steel 301 for its outstanding performance in our aircraft components, where both strength and weight savings are critical. Its formability also makes it a perfect match for our complex designs.”
Michael Brown, a surgical instrument manufacturer:
“Stainless Steel 440 is our material of choice for surgical blades. Its ability to maintain a sharp edge through repeated use ensures the reliability and precision we need in medical applications.”
Recent Studies and Research
Recent studies highlight the evolving applications and enhancements in stainless steel grades. For example, a study published in the Journal of Materials Engineering and Performance in 2023 explored the fatigue performance of Stainless Steel 301, demonstrating its enhanced lifecycle in automotive applications. Another research article in the Journal of Materials Science (2022) investigated the wear resistance of heat-treated Stainless Steel 440, affirming its superior performance in high-wear environments.
Conclusion
Choosing the right stainless steel grade for your application is crucial for ensuring optimal performance, durability, and cost-effectiveness. Stainless Steel 301 offers a balance of strength, ductility, and corrosion resistance, making it suitable for various industrial applications. In contrast, Stainless Steel 440 provides exceptional hardness and wear resistance, ideal for cutting tools and other high-wear applications.
By understanding the properties, advantages, and limitations of each grade, you can make an informed decision that aligns with your specific needs. At Tuofa, we are committed to providing high-quality stainless steel solutions tailored to meet the demands of your projects.
Additional Resources
For further information and assistance in selecting the right stainless steel for your application, feel free to contact us at Tuofa. Our team of experts is ready to provide personalized advice and support.
Comparison Table of Stainless Steel 301 vs 440
Property | Stainless Steel 301 | Stainless Steel 440 |
---|---|---|
Tensile Strength | 930 MPa (135,000 psi) | 760-1970 MPa (110,000-285,000 psi) |
Yield Strength | 520 MPa (75,000 psi) | 450-1900 MPa (65,000-275,000 psi) |
Elongation at Break | 40% | 2-20% |
Hardness (Rockwell) | B 95 max | C 58-62 |
Density | 7.93 g/cm³ | 7.75 g/cm³ |
Corrosion Resistance | Good | Fair |
Ductility | Excellent | Poor |
Wear Resistance | Moderate | Excellent |
Cost | Moderate | High |