Aluminum CNC Machining Parts
Custom Aluminum CNC Machining Service – Expert Solutions from China factory.
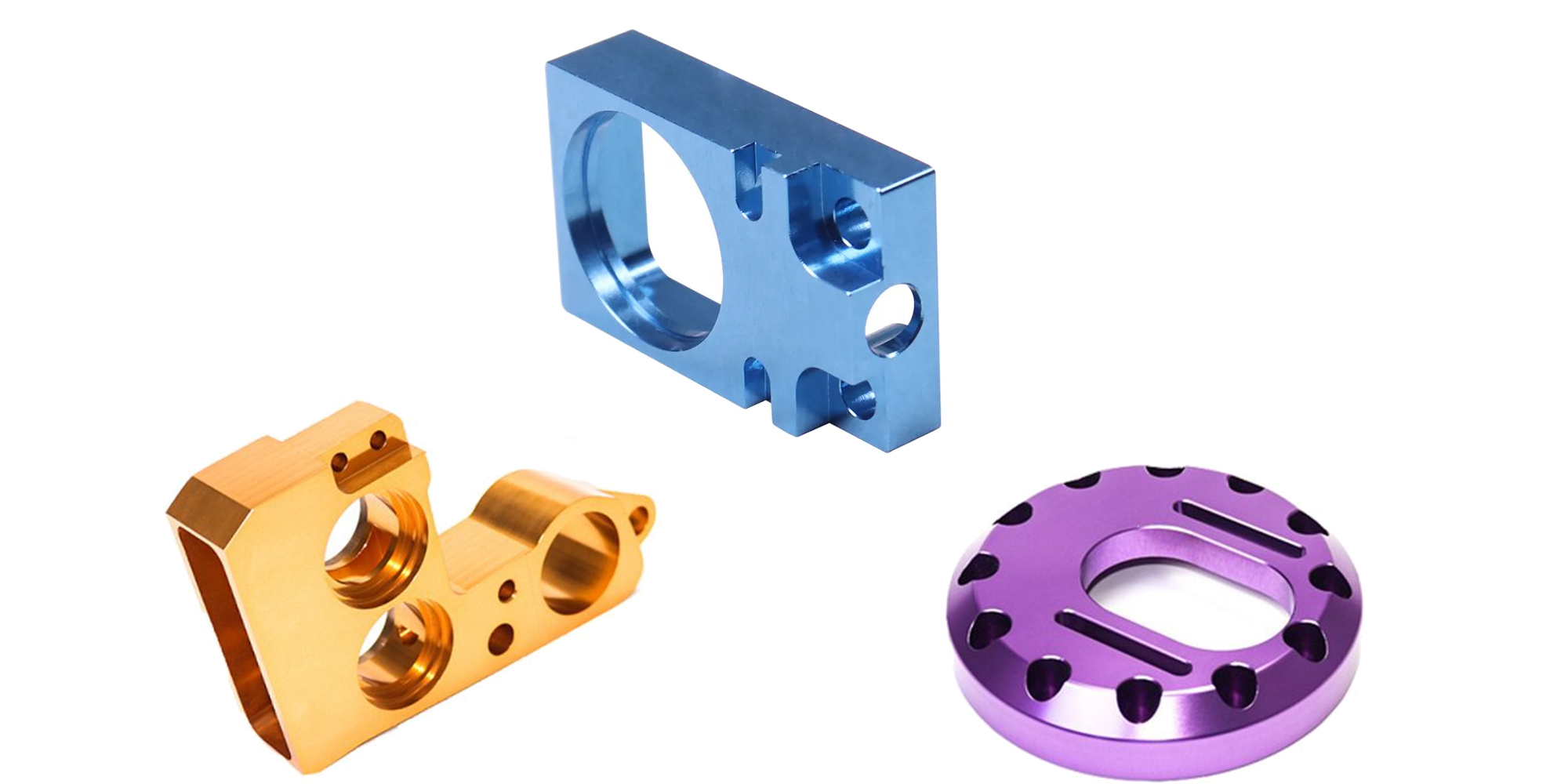
Key Benefits of Aluminum Machining in China
Strength and Lightness: Aluminum provides an excellent strength-to-weight ratio, blending durability with lightness.
Ease of Machining: It’s easily machined into complex, precise shapes, allowing for efficient production.
Corrosion Resistant: Naturally resistant to corrosion, aluminum is suitable for use in challenging environments.
Great Conductivity: With outstanding thermal and electrical conductivity, it’s essential for electronic components.
Applications of Machined Aluminum Parts
Custom machined aluminum parts are indispensable in engineering and design, offering lightweight, strong, and versatile solutions for buyers, engineers, and designers across industries. Ideal for aerospace, automotive, electronics, medical devices, robotics, and marine applications, these parts ensure optimal performance and innovation in design and functionality.
Aluminum Alloy Machining Properties
This common aluminum alloy machining chart reflects the current market preferences for various aluminum alloys, with 6061 and 7075 being most popular due to their extensive applications and excellent characteristics.
Aluminum Alloy | Density (g/cm³) | Tensile Strength (MPa) | Hardness (Brinell) | Melting Point (°C) | Elongation (%) | Mechanical Properties |
---|---|---|---|---|---|---|
6061 | 2.70 | 310 | 95 | 582-652 | 12-17 | Good mechanical properties and weldability |
7075 | 2.81 | 572 | 150 | 477-635 | 11 | High strength, less weldable |
5052 | 2.68 | 210-280 | 47 | 607-650 | 12-20 | Excellent corrosion resistance |
2024 | 2.78 | 470 | 120 | 502-638 | 10-15 | High strength, good fatigue resistance |
6063 | 2.69 | 186 | 60 | 600-650 | 12-17 | Moderate strength, good surface finish properties |
7050 | 2.83 | 510 | 135 | 490-630 | 10-14 | High strength, resistant to stress corrosion cracking |
5083 | 2.66 | 317-345 | 75 | 570-640 | 16-20 | Good strength, resistant to seawater corrosion |
Aluminium CNC Machinability by Machining Quote
Custom Aluminum Milling
Typical operations include drilling, shaping, slotting, threading, and tapering.
CNC Turning Aluminium
Operations like facing, threading, knurling, and drilling are efficiently executed, catering to bespoke design specifications.
CNC Laser Cutting
Provides precise cutting, especially for thinner materials, with high energy efficiency.
CNC Plasma Cutting
Quick and accurate, capable of cutting thick metals, widely used across multiple sectors.
CNC Waterjet Cutting
Cuts without heat, preserving material integrity, excellent for intricate designs and reducing waste.
Best Aluminum for Machining
6061 Aluminum
- Features: Excellent balance of strength, machinability, and weldability.
- Advantages: Versatile for a wide range of applications, offering good corrosion resistance and finishability.
- Considerations: While highly versatile, it may not be suitable for more demanding, high-strength applications.
7075 Aluminum
- Features: High strength-to-weight ratio, better for high-stress applications.
- Advantages: Ideal for aerospace and other industries where superior strength is critical.
- Considerations: Less weldable and more costly than other aluminum alloys like 6061.
2024 Aluminum
- Features: Known for high strength and good fatigue resistance.
- Advantages: Particularly suited for applications that endure periodic stress, like in aerospace components.
- Considerations: Not as corrosion-resistant as other alloys, often requiring protective coatings.
6 Surface Finishes for CNC Aluminum Parts
Several surface finishes are commonly used for CNC machined aluminum parts, each providing different aesthetic and functional benefits: