High Conductivity Bronze Parts with Expert CNC Machining
Discover CNC machining for high-corrosion-resistant bronze parts.
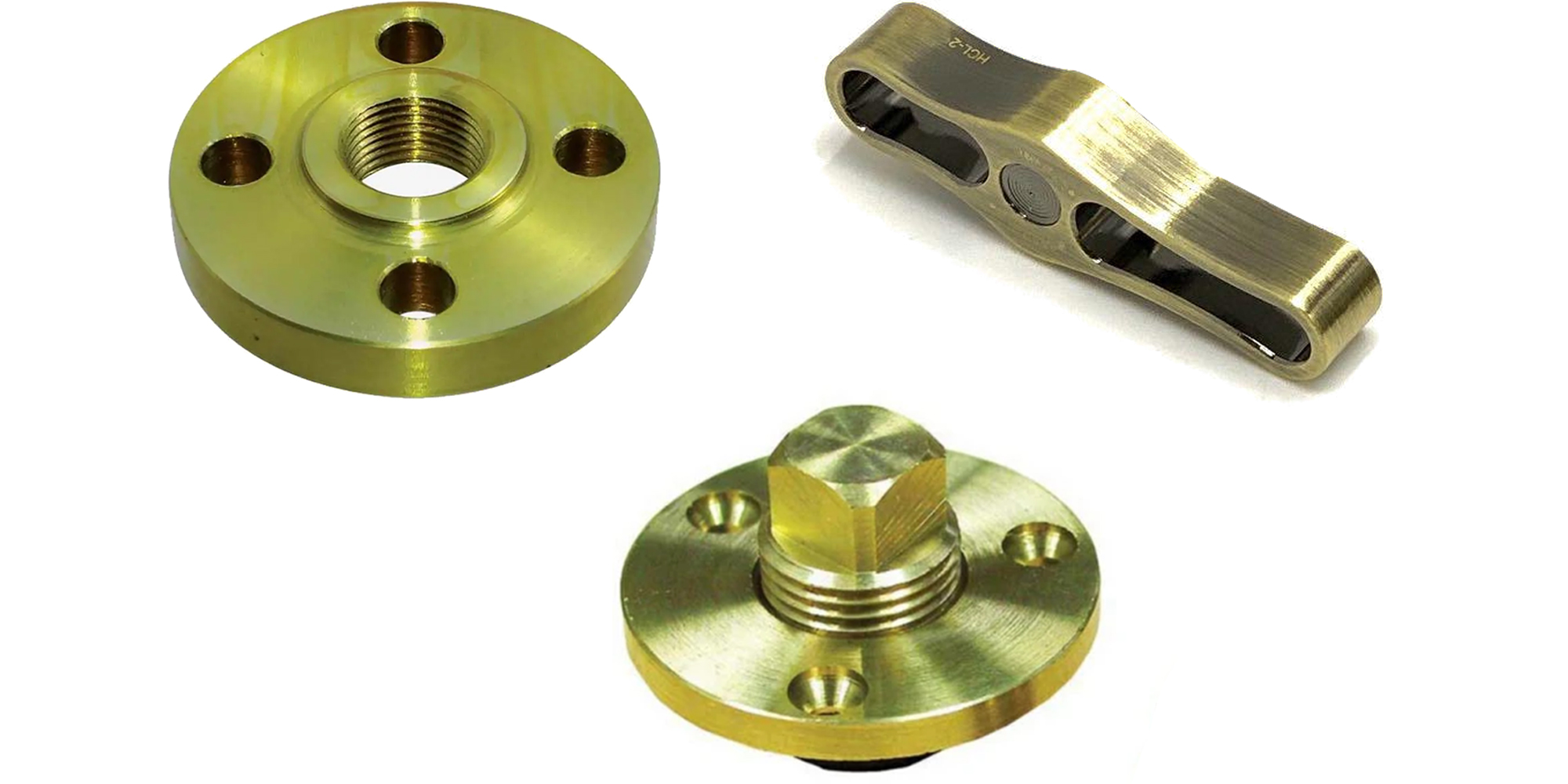
Chemical Composition of Bronze Alloys CNC Machining
Machining Quote provides a quick reference to the key chemical elements in each bronze alloy and highlights how these elements influence the alloy’s properties, which are crucial considerations for engineers and designers in selecting the right material for CNC machining projects.
ze Alloy | Tin (Sn) | Lead (Pb) | Zinc (Zn) | Aluminum (Al) | Iron (Fe) | Manganese (Mn) | Nickel (Ni) |
---|---|---|---|---|---|---|---|
C93200 (SAE 660 Bearing Bronze) | 6-8% | 6-8% | 2-4% | – | – | – | – |
C95400 (Aluminum Bronze) | – | – | – | 9-11% | 3-5% | – | 1-2% |
C86300 (Manganese Bronze) | – | – | – | 5-7.5% | 2-4% | 2.5-5% | – |
C90500 (Tin Bronze) | 10-12% | – | – | – | – | – | – |
C90700 (High Tin Bronze) | 13-14.5% | – | 0.20-0.50% | – | – | – | – |
Bronze Machinability Chart
These properties are essential when selecting a bronze alloy for specific CNC machining projects, as they directly influence the machining process, the performance of the machined parts, and their suitability for different environments or mechanical stresses.
Bronze Alloy | Density (g/cm³) | Tensile Strength (psi) | Hardness (Brinell) | Elongation (%) | Thermal Conductivity (W/m·K) | Coefficient of Thermal Expansion (µm/m·K) |
---|---|---|---|---|---|---|
C93200 (SAE 660 Bearing Bronze) | 8.8 | 35,000 | 65-75 | 10 | 60 | 18.3 |
C95400 (Aluminum Bronze) | 7.45 | 85,000 | 170-210 | 12 | 38.1 | 16.0 |
C86300 (Manganese Bronze) | 7.83 | 110,000 | 225 | 14 | 58.2 | 17.5 |
C90500 (Gun Metal, Tin Bronze) | 8.8 | 45,000 | 75-90 | 20 | 59.9 | 18.7 |
C90700 (High Tin Bronze) | 8.89 | 45,000 | 90-110 | 10 | 52.0 | 19.2 |
CNC Machining Bronze Types and Applications
Surface treatments are applied to increase the surface hardness, reduce friction, and enhance corrosion resistance. Common treatments include:
C93200 (SAE 660 Bearing Bronze)
Primarily used for fabricating bearings, bushings, and wear plates in machinery and automotive applications.
C95400 (Aluminum Bronze)
Commonly used for high-strength parts such as gears, valves, valve stems, and marine hardware that require excellent corrosion resistance.
C86300 (Manganese Bronze)
Ideal for constructing heavy-load bearings, heavy-duty gears, and components in construction equipment and heavy machinery.
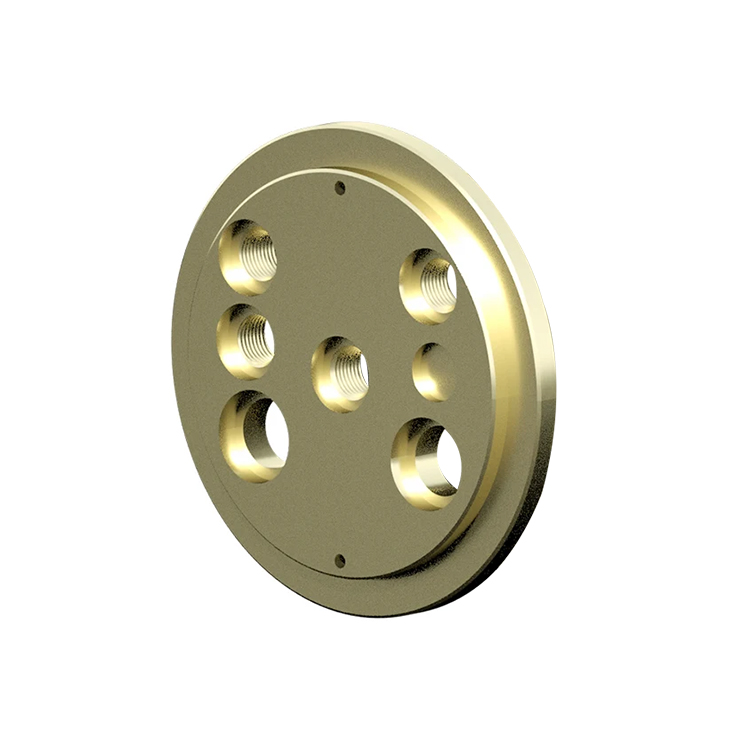
C90500 (Gun Metal, Tin Bronze)
Typically used for gears, bearings, pump impellers, and piston rings where strength and resistance to wear are essential.
C90700 (High Tin Bronze)
This process softens the steel, making it easier to machine or form. After CNC machining, re-annealing can be done to relieve internal stresses and enhance machinability.
C64200 (Aluminum Silicon Bronze)
Frequently used in aerospace for fasteners, and marine applications for bolts, nuts, and screws due to its strength and resistance to saltwater corrosion.
Ampco 18 and C95400 Aluminum Bronze are both strong and corrosion-resistant, but here are some simple differences:
- Strength: Ampco 18 is generally stronger than C95400.
- Hardness: Ampco 18 is also harder, which means it’s better at resisting wear.
- Machinability: C95400 is easier to machine, making it less challenging to work with.
- Cost: Ampco 18 is usually more expensive due to its superior properties.
Both are good choices, but the best one depends on your specific needs, like how tough the material needs to be or your budget.