Custom Sheet Metal Welding Services in China Supplier
Enhance your project with our Custom Sheet Metal Welding Services, offered by Machining Quote China Supplier. We leverage advanced technology and skilled craftsmanship to deliver durable and precise metal components tailored to your requirements.
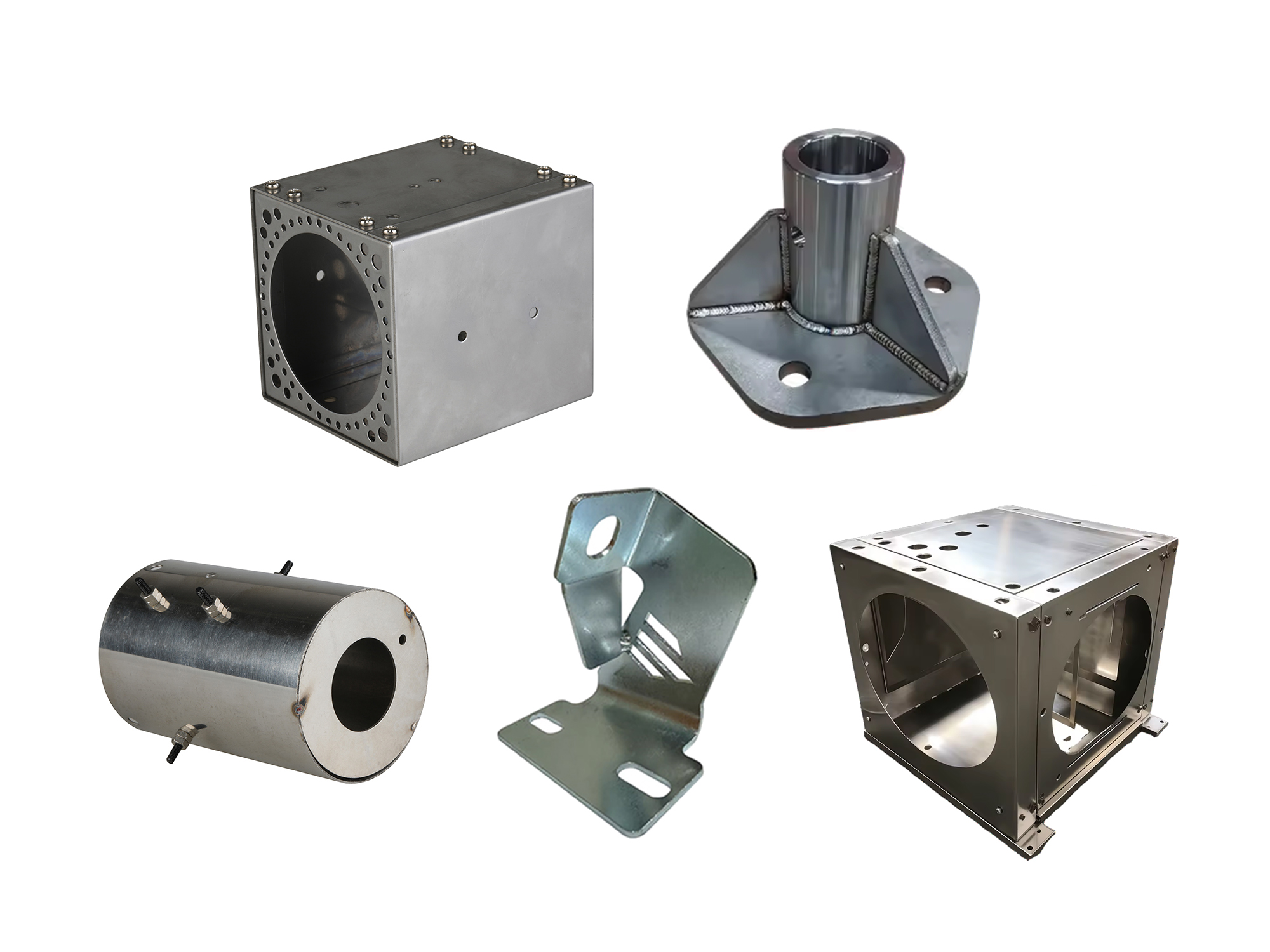
Pros and Cons of Metal Welding Parts
Advantages | Disadvantages |
---|---|
Structural Integrity | Precision Requirement |
Provides exceptionally strong and durable joints ideal for critical load-bearing applications. | Demands high precision in execution; minor errors can compromise structural integrity. |
Design Flexibility | Thermal Distortion |
Allows for the joining of complex shapes and designs, expanding creative possibilities. | Heat from welding can cause warping or distortion, requiring careful planning to mitigate. |
Economical for Mass Production | Specialized Equipment Needed |
Cost-effective for large-scale production due to lower material costs and potential for automation. | Requires investment in specific welding equipment and maintenance which can be costly. |
Seamless Finish | Material Sensitivities |
Can achieve a smooth and clean finish that enhances the product’s aesthetic appeal. | Not all materials are weldable; some may require special techniques or cannot be welded at all. |
Durability in Joining Dissimilar Metals | Inspection and Testing Demands |
Capable of effectively joining different metals, which can be crucial in multi-material designs. | Welds often require rigorous inspection and testing to ensure they meet safety and quality standards. |
Precision Metal Welding Parts and Products
Precision metal welding allows your products to meet the high standards demanded by advanced applications, ensuring that parts and products perform as expected under critical conditions.
Types Of Metal Welding
Metal welding is a fundamental technique in manufacturing and construction, with several types suited to different applications and material types. Here’s an overview of the most common welding processes:
Materials of Sheet Metal Welding
Aluminum
Aluminum is a lightweight, corrosion-resistant metal ideal for applications requiring a high strength-to-weight ratio and good thermal conductivity. It’s easy to machine and extensively used in aerospace, automotive, and consumer electronics. Common types of aluminum alloys like 6061 and 7075 offer enhanced mechanical properties, such as improved toughness and hardness.
- Price: $$
- Lead Time: 10 days
- Wall Thickness: 0.75 mm
- Tolerances:+/-0.125mm (±0.005″)
- Max part size: 200 x 80 x 100 cm
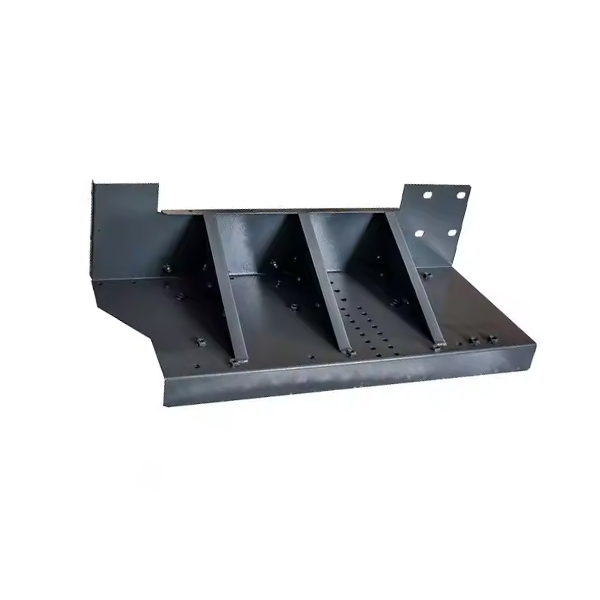
Copper
Copper is highly conductive to both heat and electricity, making it popular in electrical applications, heat exchangers, and automotive parts. It is relatively easy to machine and provides a unique combination of ductility, strength, and thermal conductivity. Its natural resistance to corrosion and aesthetic appeal also make it a choice material for decorative applications.
- Price: $$$
- Lead Time: =10 days
- Wall Thickness: 0.75 mm
- Tolerances: plusmn;0.125mm (±0.005″)
- Max part size: 200 x 80 x 100 cm
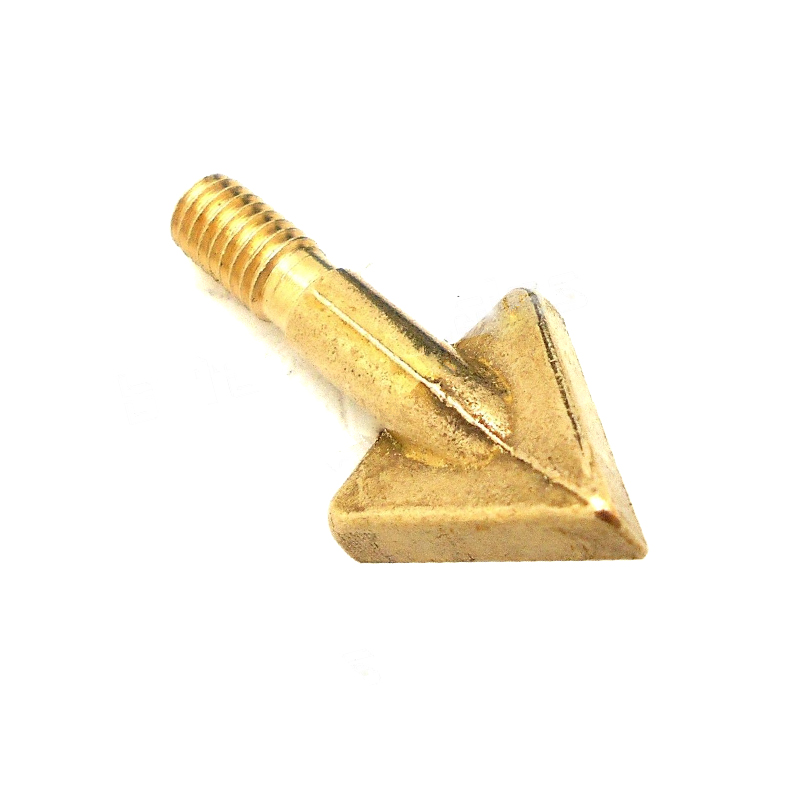
Brass
Brass is an alloy of copper and zinc, known for its machinability and corrosion resistance. It’s often used for decorative items, plumbing fixtures, electrical components, and musical instruments. Brass provides a balance between strength and ductility and can be easily machined into complex shapes.
- Price: $$$
- Lead Time: < 10 days
- Wall Thickness: 0.75 mm
- Tolerances: ±0.125mm (±0.005″)
- Max part size: 200 x 80 x 100 cm
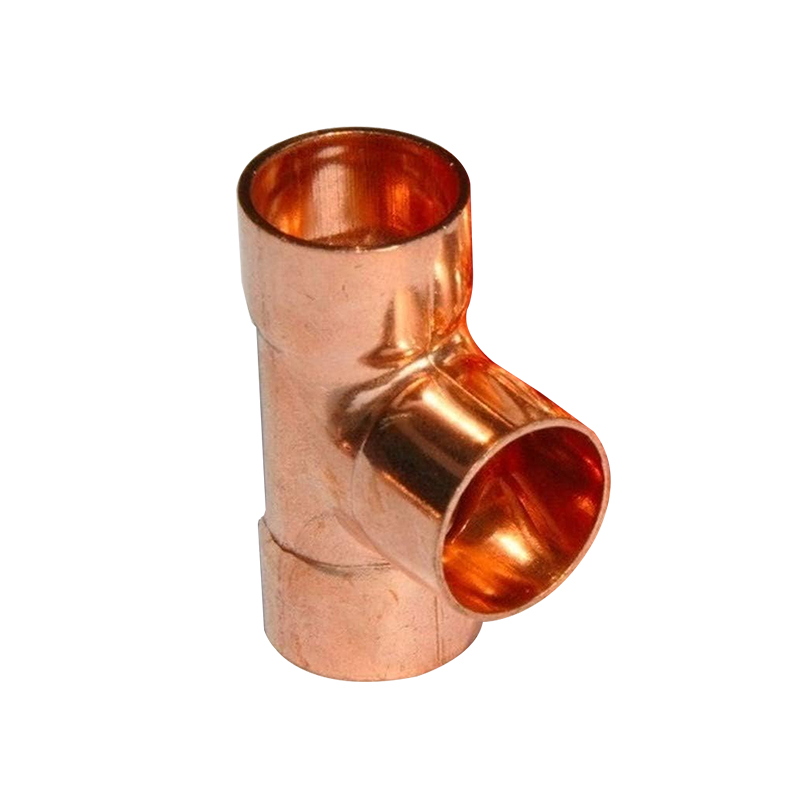
Stainless Steel
Stainless Steel is renowned for its corrosion resistance and strength. It’s widely used in food processing equipment, medical devices, and general metal fabrication. Stainless steel alloys, like 304 and 316, offer a good balance of corrosion resistance, machinability, and cost-effectiveness. It’s a versatile material suitable for a wide range of applications.
- ?Price: $$
- ?Lead Time: < 10 days
- ?Wall Thickness: 0.75 mm
- ?Tolerances: ±0.125mm (±0.005″)
- ?Max part size:200 x 80 x 100 cm
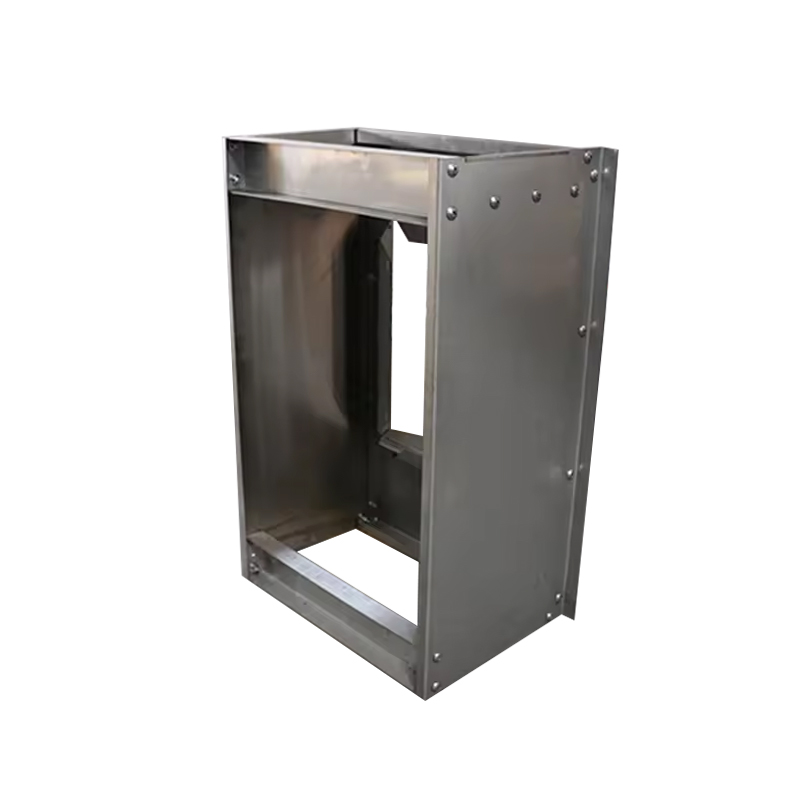
Titanium
Titanium is known for its exceptional strength, lightweight, and high corrosion resistance. It’s often used in aerospace, medical implants, and high-performance automotive applications. Titanium is challenging to machine but offers superior mechanical properties and a very high strength-to-weight ratio, making it ideal for advanced engineering applications.
- ?Price: $$$$$
- ?Lead Time: < 10 days
- ?Wall Thickness: 0.75 mm
- ?Tolerances: ±0.125mm (±0.005″)
- ?Max part size: 200 x 80 x 100 cm
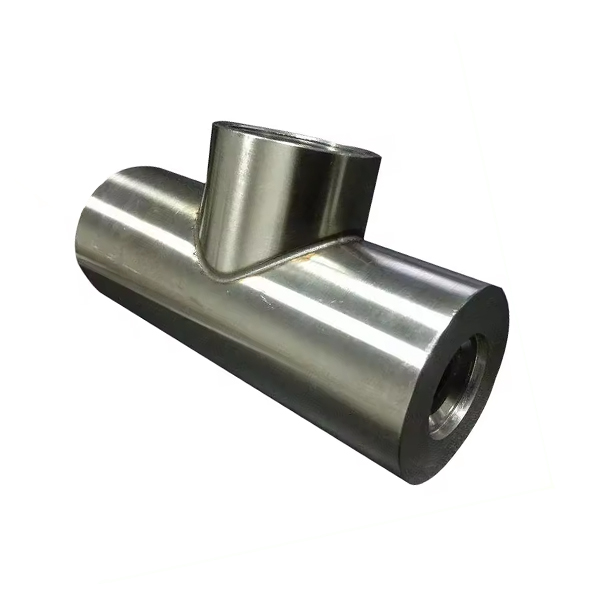
Sheet Metal Welding Process: Custom and Support
Sheet metal welding for custom and support structures requires a blend of skilled labor, precise equipment, and careful planning. Whether creating a one-off custom piece or mass-producing components, the welding process must be adapted to meet specific requirements while maintaining high standards of quality and functionality.
Stage | Description |
---|---|
Design Consultation | Collaboration between engineers and designers to ensure the welding process meets design and functional needs. |
Material Selection | Choosing the appropriate type of sheet metal based on the project's aesthetic and structural requirements. |
Prototyping | Creating initial prototypes to test welding specifications and adjust the design before full-scale production. |
Setup Preparation | Assembling specialized equipment or fixtures to accommodate unique shapes, sizes, or designs. |
Welding Execution | Carrying out the welding process, ensuring precision and adherence to design specifications. Voltage: 10-35V, Amperage: 50-250A, Wire Speed (MIG): 100-400 IPM |
Heat Management | Implementing strategies to manage heat input and distribution to avoid warping and ensure integrity. Gas Flow Rate: 15-25 L/min, Travel Speed: 8-12 inches per minute |
Quality Control | Inspecting and testing welded joints for strength, appearance, and compliance with standards. |
Post-Weld Treatment | Applying treatments such as stress relieving or heat treatment to improve mechanical properties and reduce stress. |
Post Processing Services for Sheet Metal Stamping Parts
Proper post-processing not only enhances the welded product's appearance but also significantly boosts its performance and lifespan.
Heat Treatments
Stress Relieving: Reduces residual stresses in the weld area to improve mechanical properties and prevent distortion.
Annealing: Softens the metal, making it more workable and enhancing its ductility.
Hardening and Tempering: Increases the hardness and strength of the metal, followed by tempering to achieve desired toughness.