Advance Projects with PEEK CNC Machining Parts
Partner with Machining Quote to elevate your designs using PEEK high temperature resistance, and mechanical strength, ensuring peak quality and efficiency.
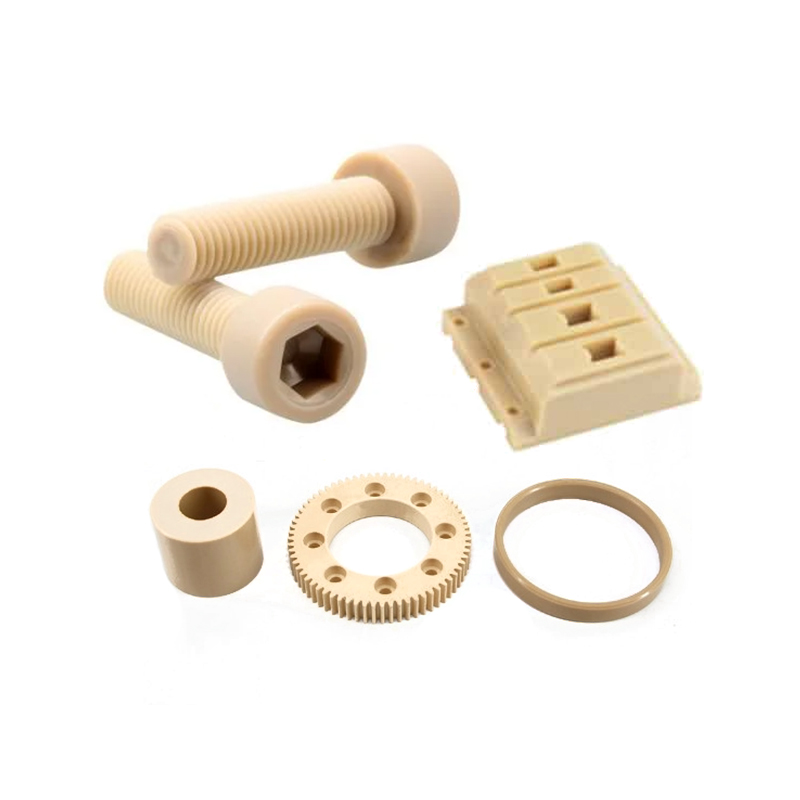
Merits of PEEK Plastic CNC Machining
PEEK Machining Tolerances +/- . 0005 by Machining Quote: This enables the realization of intricate and complex designs to precise tolerances. Beyond ISO 2768-m
High Performance and Durability: PEEK withstands harsh conditions like high temperatures and chemicals, ensuring your designs last longer without degradation.
Lightweight Advantage: Experience the transformative lightweight property of PEEK, a stark contrast to heavier metals. This attribute is particularly advantageous in sectors like aerospace and automotive engineering, where every gram counts.
Cost-Effectiveness Over Time: Initially, PEEK materials might seem more expensive, but their longevity and the reduced maintenance they require offer significant cost benefits in the long run.
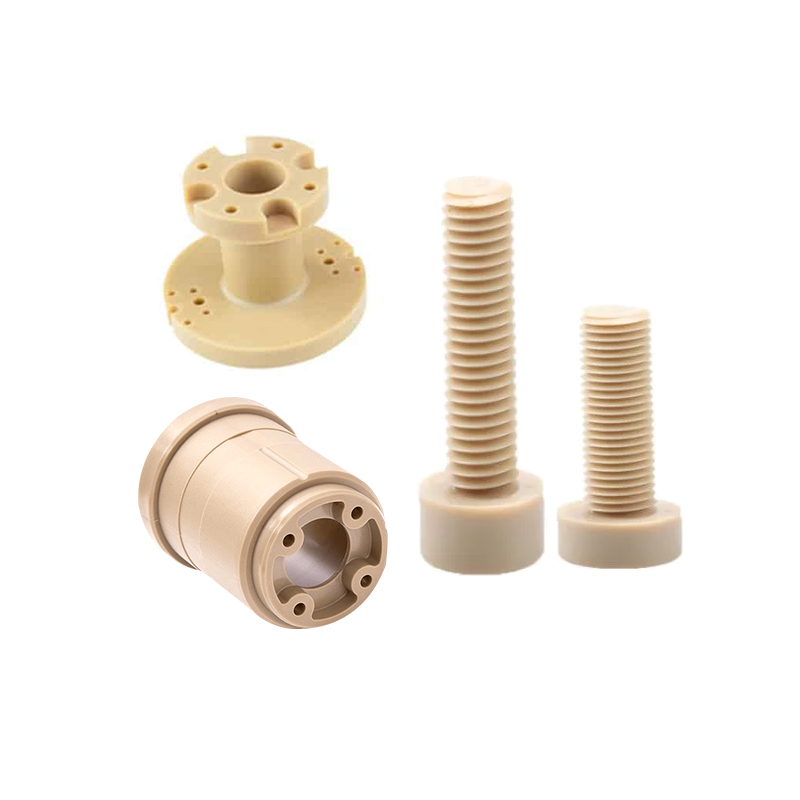
Industries of CNC Machining PEEK
These applications showcase the adaptability of PEEK to high-stress, high-precision tasks, making it a cornerstone material in advanced manufacturing.
- Aerospace: Valves, seals, bushings, and insulation components.
- Medical Devices: Surgical instruments, dental implant parts, and prosthetic limbs.
- Electronics: Insulators, connectors, and components for semiconductor machinery.
- Automotive: Gears, pumps, and thrust washers in high-performance vehicles.
- Food Processing: Non-toxic and compliant components like gears and bushings that require chemical resistance.
- Oil and Gas: Seals, back-up rings, and compressor parts resistant to extreme temperatures and corrosive environments.
Machinability of PEEK Plastic
it’s important to note that these values can vary based on the grade of PEEK and its processing conditions. Here is a generalized example based on typical values found in standard grades of PEEK:
PEEK Properties | Description | Typical Values |
---|---|---|
Tensile Strength, Yield (MPa) | Measures the maximum stress PEEK can handle before deforming, crucial for structural integrity. | 90-100 MPa |
Heat Deflection Temperature (°C) | Temperature at which PEEK deforms under load, important for applications involving high heat. | 150-160 °C |
Chemical Resistance | Ability to withstand aggressive chemicals, essential for harsh environments like chemical processing. | Excellent resistance to a wide range of chemicals |
Tensile Modulus | Indicates the stiffness and mechanical strength, important for applications requiring rigidity. | 3,700-4,000 MPa |
Impact Strength | Measures the material’s capability to withstand sudden and severe impacts, critical in dynamic environments. | 7-16 kJ/m^2 |
Glass Transition Temperature (°C) | Temperature at which the material softens from a glassy to a rubbery state, affecting thermal stability. | 143 °C |
PEEK CNC Machining Processing by Machining Quote
CNC Turning PEEK
Carbide and ceramic cutting tools are commonly used for PEEK turning to provide better wear resistance and higher machining speeds.
CNC Milling PEEK
Choosing the right milling cutters, such as ball-end mills and flat-end mills, and optimizing the tool path, ensures high material utilization and minimal waste, especially suitable for expensive PEEK materials.
PEEK CNC Grinding
CNC Drilling PEEK enables extremely high hole positioning accuracy, which is important in many high-performance applications such as aerospace and medical devices
PEEK Plastic Machining Speeds and Feeds
Here is a detailed table of machining parameters for Natural PEEK and Carbon-Fiber-Reinforced PEEK, covering various CNC processes:
CNC Machining Process | Material | Preheat (if necessary) | Clearance Angle (degrees) | Rake Angle (degrees) | Cutting Speed (m/min) | Feed Rate (mm/rev) |
---|---|---|---|---|---|---|
Drilling | Natural PEEK | 120°C | 5 to 10 | 10 to 30 | 50 to 200 | 0.1 to 0.3 |
Carbon-Fiber-Reinforced PEEK | 120°C | 6 | 5 to 10 | 80 to 100 | 0.1 to 0.3 | |
Milling | Natural PEEK | None | 5 to 10 | 10 to 30 | 50 to 200 | Variable* |
Carbon-Fiber-Reinforced PEEK | None | 15 to 30 | 10 to 15 | 200 to 300 | Variable* | |
Turning | Natural PEEK | None | 6 to 8 | 0 to 5 | 250 to 500 | 0.1 to 0.5 |
Carbon-Fiber-Reinforced PEEK | None | 6 to 8 | 2 to 8 | 150 to 200 | 0.1 to 0.5 |
Surface Finishes for CNC Peek Parts
For your CNC machined PEEK parts, we offer a range of surface finishes, ensuring your components not only meet precise functional specifications but also achieve the desired aesthetic appeal.