High Precision Tool Steel Machining
Carbon steel is an alloy primarily composed of iron and carbon, with carbon content typically ranging from 0.04% to 2.5%. This composition allows us to categorize carbon steel into three types: low-carbon steel (usually less than 0.3% carbon), medium-carbon steel (about 0.3% to 0.6% carbon), and high-carbon steel (0.6% to 2.5% carbon).
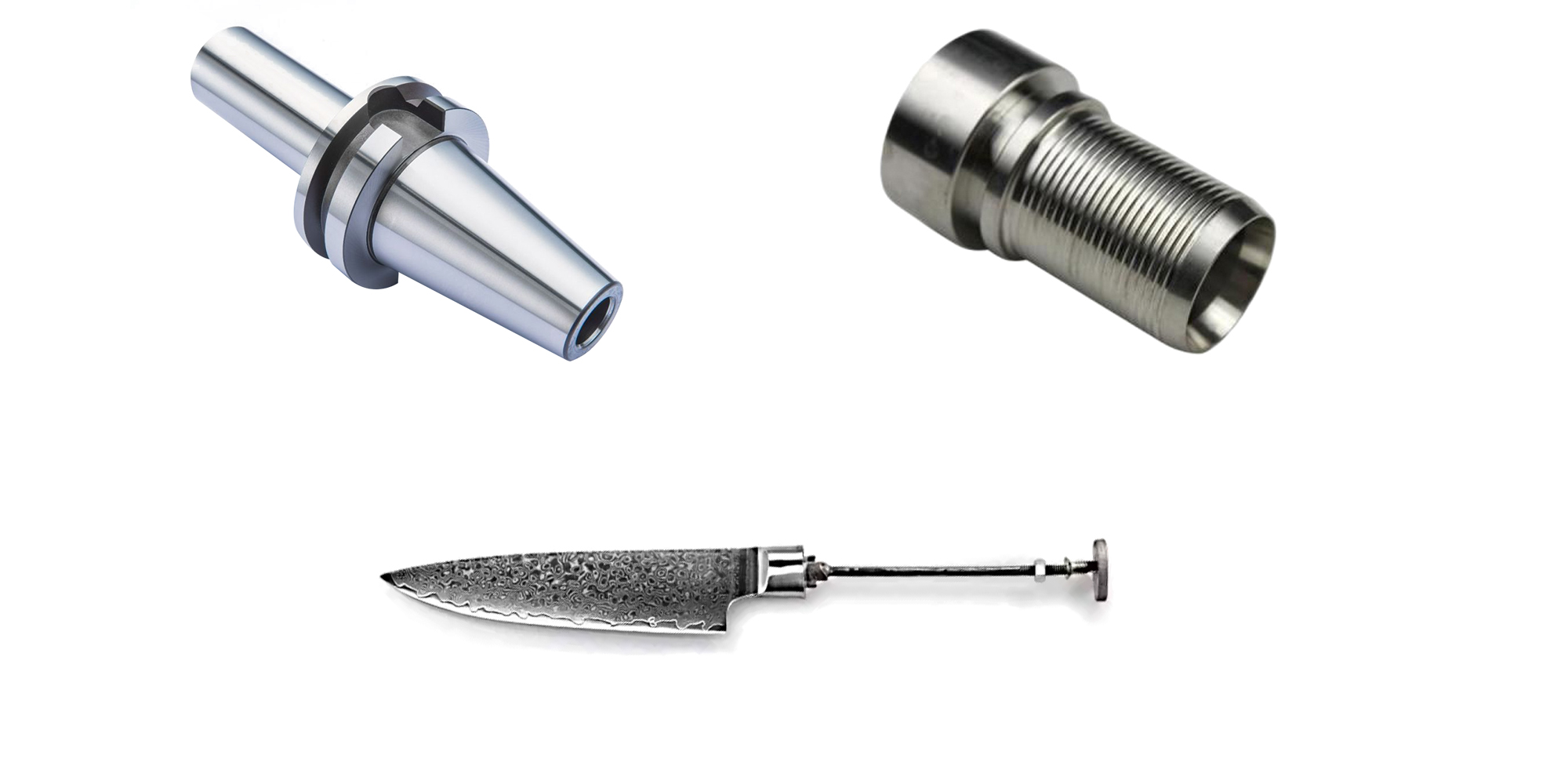
Tool Steel Machining Properties
This table reflects the standard alloy percentages, but actual content may vary based on the manufacturer and specific applications.
Tool Steel Grade | Carbon (C) | Tungsten (W) | Molybdenum (Mo) | Vanadium (V) | Chromium (Cr) | Cobalt (Co) | Manganese (Mn) |
---|---|---|---|---|---|---|---|
M2 | 0.85% | 6.35% | 5.00% | 1.85% | 4.15% | – | 0.30% |
M42 | 1.10% | 1.50% | 9.50% | 1.15% | 3.75% | 8.00% | 0.30% |
D2 | 1.50% | – | 0.60% | 0.90% | 11.50% | – | 0.60% |
A2 | 1.00% | – | 1.00% | 0.25% | 5.25% | – | 1.00% |
H13 | 0.40% | – | 1.25% | 1.00% | 5.25% | – | 0.40% |
H11 | 0.36% | – | 1.50% | 0.60% | 5.00% | – | 0.40% |
Physical Properties of CNC Machining Tool Steels
This version of the table focuses on properties that directly impact the performance and lifetime of tool steels under operational conditions, especially during high-speed or high-temperature machining.
Tool Steel Grade | Hardness (HRC) | Toughness (Joules) | Wear Resistance | Thermal Stability | Thermal Conductivity (W/m·K) |
---|---|---|---|---|---|
M2 | 60-65 | Medium | High | Good | 25-30 |
M42 | 65-70 | High | Very High | Excellent | 20-25 |
D2 | 55-62 | Low | Very High | Fair | 15-20 |
A2 | 57-62 | High | High | Good | 18-22 |
H13 | 50-55 | Very High | High | Excellent | 24-28 |
H11 | 50-54 | Very High | High | Excellent | 23-27 |
CNC Machining Tool Steel Types and Applications
In CNC machining, different types of tool steels are selected based on their properties to craft various components. Here are some typical tool steel types and the specific parts they are used to make:
High-Speed Steel (HSS)
Drill Bits and End Mills: High-Speed Steel is extensively used for manufacturing drill bits and end mills used in CNC machining. These tools need to withstand high temperatures and resist wear, qualities that HSS offers, enabling them to perform precise and efficient cutting operations.
Taps and Dies: HSS is also used to manufacture taps and dies for threading operations. Its toughness and hardness make it ideal for cutting threads in metals without losing sharpness quickly.
Die Steel
Injection Molding Tools: Die steel is commonly used for fabricating high-precision molds for injection molding. Its wear resistance and ability to maintain dimensional stability under high pressure and temperature conditions make it suitable for producing complex and detailed plastic parts.
Stamping Dies: Stamping dies made from die steel are used to cut and form sheet metal into specific shapes. The durability and strength of die steel allow these dies to operate under high-stress conditions, producing parts with high repeatability.
Tool Steel (General)
Gear Cutters: Tool steels are used to make gear cutters, which need to be hard and wear-resistant to accurately cut gear teeth in materials like brass and steel.
Punches and Dies: Used in the sheet metal industry for punching operations, these components benefit from the high hardness and toughness of tool steels, ensuring long life and precision in high-volume manufacturing environments.
Surface Treatment of CNC Machining Carbon Steel
Surface treatments are applied to increase the surface hardness, reduce friction, and enhance corrosion resistance. Common treatments include:
Nitriding
This process introduces nitrogen into the surface of the steel, forming a hard, wear-resistant layer. It’s particularly beneficial for components like gears and spindles, which are subject to high wear.
Carburizing
By adding carbon to the surface, this treatment greatly increases surface hardness and overall wear resistance. It’s ideal for high-stress parts like camshafts and crankshafts.
Coating (e.g., TiN, TiCN, AlTiN)
These coatings significantly reduce friction and increase hardness, allowing higher cutting speeds and prolonged tool life. They are excellent for drill bits and milling cutters.
Heat Treatment
Heat treatment processes like hardening and tempering are used to adjust the microstructure of tool steels, improving toughness, hardness, and wear resistance.
Hardening and Tempering
This process involves heating the steel to a high temperature, followed by rapid cooling (quenching) and reheating (tempering). This results in a tool that is both hard and tough, suitable for cutting and forming applications.
Annealing
This process softens the steel, making it easier to machine or form. After CNC machining, re-annealing can be done to relieve internal stresses and enhance machinability.