精密镁加工服务
我们拥有先进的镁加工技术,可满足航空航天、汽车和科技行业的严格要求,让您体验顶级精度。
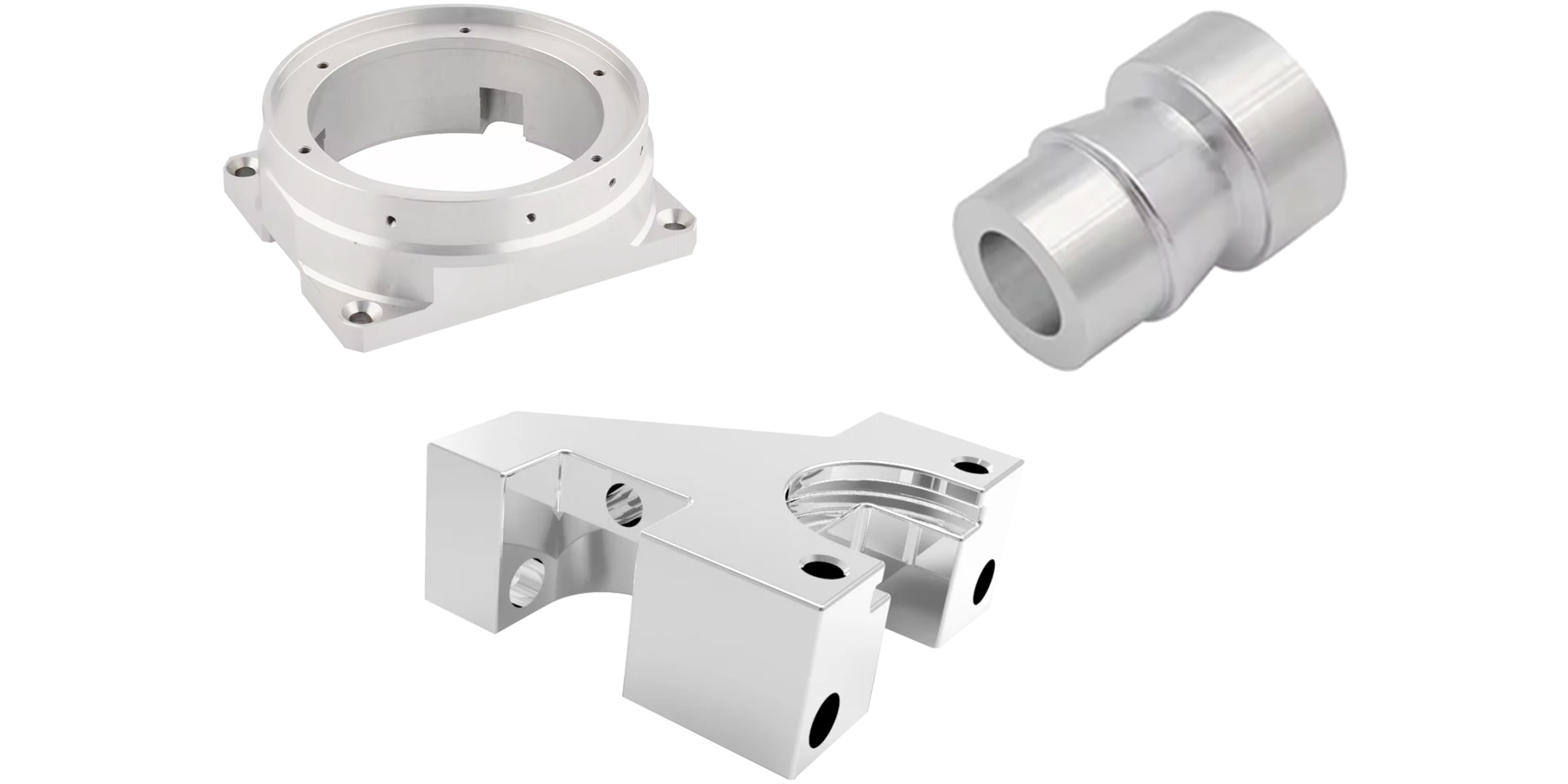
镁合金 CNC 零件的优缺点
镁合金 | 优点 | 缺点 | ASTM 标准 |
---|---|---|---|
AZ31B | 重量轻、强度高;良好的可焊性和可加工性;适度的耐腐蚀性 | 点火风险较高;耐磨性较低;高温性能有限 | ASTM B90/B90M |
AZ91D | 高强度和优异的铸造性能;良好的耐腐蚀性;适用于复杂的形状 | 与非铸造合金相比,延展性较低;加工过程中存在易燃性问题 | ASTM B94 |
AM60B | 冲击韧性高;铸造性能好;强度和硬度适中 | 抗蠕变性较低;高温性能降低 | 对于某些形式,通常采用 ASTM B90 标准,但主要是一种铸造合金,没有针对所有形式的特定 ASTM 标准。 |
WE43 | 强度高,尤其是在高温条件下;耐腐蚀性和可焊性好;适用于高温应用场合 | 加工成本较高;加工难度较大 | ASTM B80 |
ZE41 | 优异的铸造和机械性能;良好的抗冲击和耐腐蚀性;适用于复杂铸件 | 高温下性能更易下降;强度和硬度相对较低 | ASTM B80 |
数控镁零件和配件
这些例子凸显了数控镁合金零件在各种高需求行业中提高性能和功能的关键作用。
镁合金的化学成分
本表简要概述了每种镁合金中的主要合金元素,这对于了解它们的基本特性和在数控加工中的各种应用的适用性至关重要。
镁合金 | 组成 |
---|---|
AZ31B | 镁-3%铝、1%锌、0.3%锰 |
AZ91D | 镁-9%铝、1%锌、0.2%锰 |
AM60B | 镁-6%铝,0.5%锰 |
WE43 | 镁钇稀土-Zr |
ZE41 | 镁-4%锌、1% 稀土(主要是铈)、0.7%锆 |
机加工合金的主要机械性能
本表采用了这些合金的常用参考数据,为涉及镁合金数控加工的工程项目中的材料选择提供了可靠的依据。
镁合金 | 密度(克/立方厘米) | 拉伸强度(兆帕) | 屈服强度(兆帕) | 伸长率 (%) | 硬度 (HB) |
---|---|---|---|---|---|
AZ31B | 1.78 | 240 | 160 | 15 | 65 |
AZ91D | 1.81 | 290 | 250 | 3 | 70 |
AM60B | 1.80 | 235 | 130 | 8 | 60 |
WE43 | 1.84 | 280 | 180 | 8 | 75 |
ZE41 | 1.83 | 250 | 140 | 6 | 65 |
数控镁加工工艺
在 加工报价, we elevate CNC machining of copper to new heights, offering tailored CNC turning and CNC milling solutions that empower you, our engineering and design partners, to push the boundaries of innovation and precision.
数控车削
数控车削是一种快速、精确的镁合金成型方法。在此过程中,金属在旋转,而固定的工具将其切割成形。镁很轻,因此我们可以快速高效地车削它。但是,镁在切割时很容易着火。为了避免这种情况,我们采用特殊的冷却方法来控制热量,并安全地处理从金属上脱落的微小碎屑。
数控铣床
数控铣利用旋转工具在镁块上雕刻出细致的形状。这种方法非常适合快速制作复杂的设计,因为镁很容易切割。与车削一样,镁有起火的危险,这意味着我们必须小心控制热量。我们在铣削过程中使用冷却剂,以保证一切安全顺利。
数控铜零件的表面处理
数控镁合金零件的表面处理因应用、功能和美学要求的不同而有很大差异。
最容易加工的铜一般被认为是 110 铜,也称为电解韧性铜 (ETP)。它的导电率为 100% IACS,具有很好的延展性,硬度不如其他铜合金,因此更容易使用数控加工方法进行切割和成型。因此,铜 110 在要求高精度和易加工性的行业中很受欢迎。